Table of Contents
The Zenith INAT Carburetor used on all six cylinder, carbureted, U. S. specification BMWs was introduced in 1969, and is a two-stage model with an automatic choke and a vacuum-operated second stage.
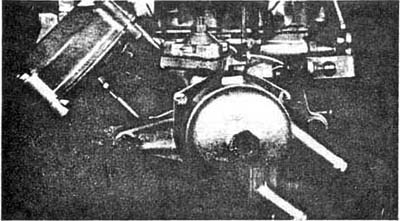
This is the automatic choke, which uses both engine coolant and electric power to control the choke for warm up.
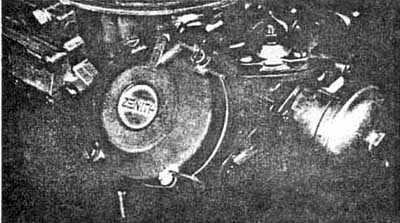
This is the second stage vacuum box and linkage.
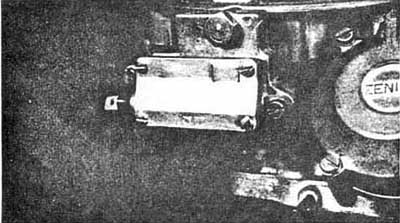
This is the electrically operated cold-start valve.
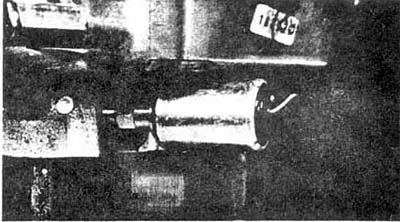
And this is the idle shut-off valve.
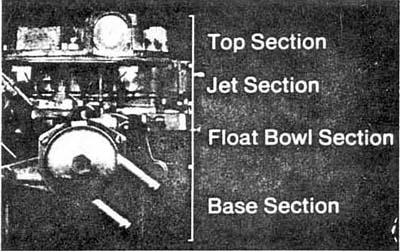
The carburetor is constructed in four layers: the Top Section, the Jet Section, and Float-Bowl Section, and the Base.
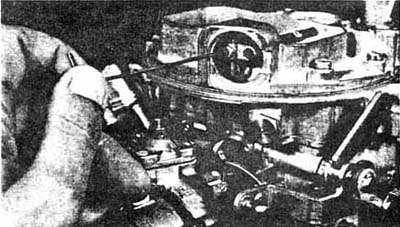
Loosen the 1.5 mm Allen screw ... or the set screw on earlier models, and disconnect the choke connecting rod.
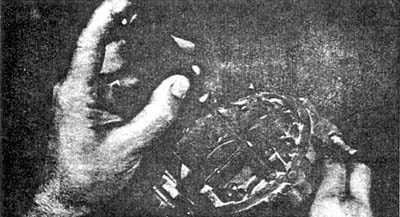
Now, remove the nine screws on top. Eight are around the outside: the ninth is in the center, underneath the air cleaner stud. Note the position of the three longer screws.
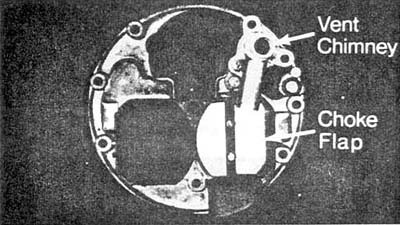
The top contains the Choke Flap and the Vent Chimney.
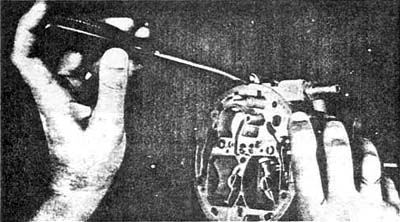
The Jet Section is removed by taking out the three screws on top. The Cold Start Valve must also be removed.
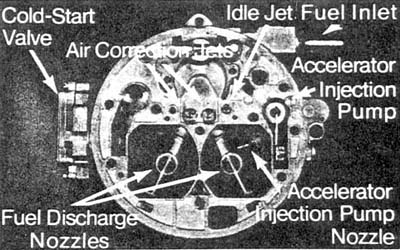
On top is the Cold-Start Valve, the Air Correction Jets, the Idle Jet, the Accelerator Injection Pump, the Fuel Inlet, the Accelerator Injection Nozzle in the First Stage, and the First and Second Stage Fuel Discharge Nozzles.
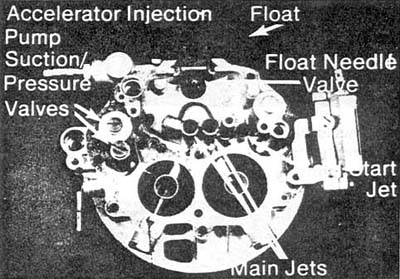
On the bottom of the Jet Section is the Float and Float Needle Valve, the Main Jets, the Cold-Start Jet, and the Accelerator Injection Pump Suction and Pressure Valves.
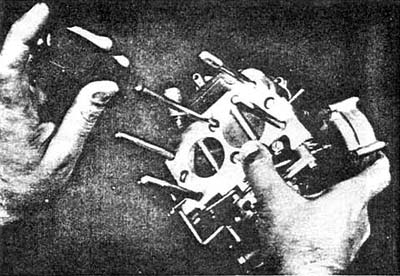
Four screws in the Base Section hold the Float-Bowl Section and Base together.
The plastic connection link and the Second Stage Vacuum Box linkage rod must also be removed before the two can be separated.
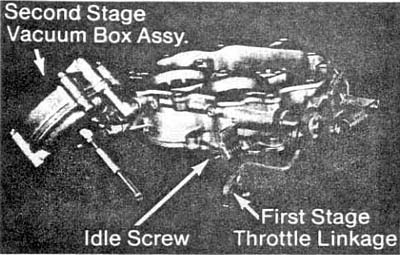
The Float-Bowl Section contains part of the First Stage Throttle Linkage, the Idle Screw, and the Second Stage Vacuum Box and Connecting Rod.
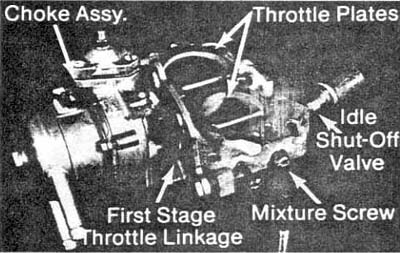
The Base, or Throttle Plate Section, contains the remainder of the First Stage Throttle Linkage, the Second Stage Throttle Linkage, the First and Second Stage Throttle Plates, the Choke Assembly, the Idle Shut Off Valve, and the Mixture Screw.
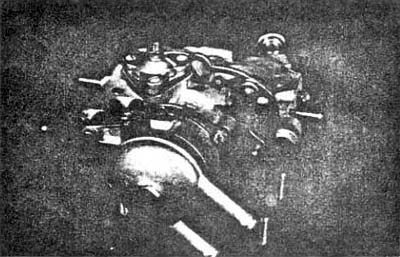
On top of the Choke Housing is the Choke Pull Down Vacuum Box. As soon as the engine cranks, vacuum from below the throttle plate pulls the choke plunger up to open the choke 3 mm.
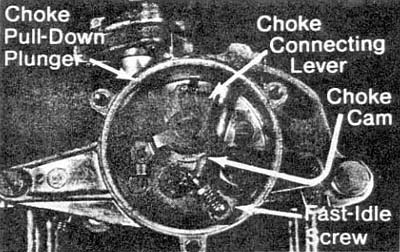
Remove the three screws holding the choke cover in place. Inside is the Choke Pull-Down Plunger, the Choke Connecting Lever, the Choke Cam, and the Fast-Idle Screw.
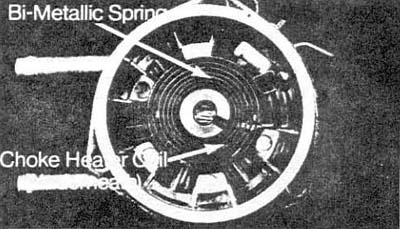
Inside the cover itself is the Bi-Metallic Spring, and, beneath the Spring, the Choke Heater Coil
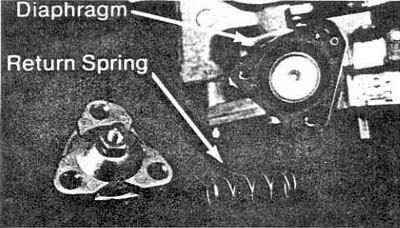
Inside the Vacuum Box is the Pull-Down Diaphragm and Return Spring. Adjustments are made with the screw and lock nut on the vacuum box cover.
Begin with the first and second layers removed from the Float-Bowl and Base Sections. There are a number of external adjustments on this part of the carburetor.
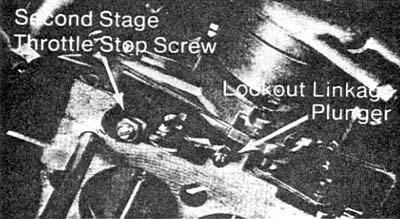
Behind the choke housing is the second stage linkage. There are two adjusting screws on the bottom of this linkage: the second stage throttle stop and the Lock-Out Linkage Plunger which sets tension on the first stage linkage cam.
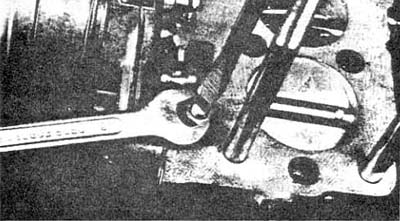
If necessary, adjust the throttle plate stop screw so the plate is closed, but not binding.
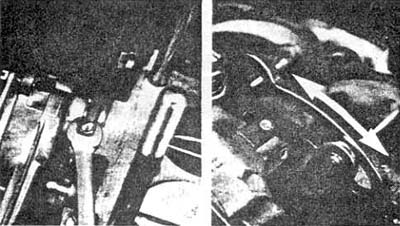
Back off the lock nut and adjust the plunger screw so the first stage roller moves freely through its guide.
In front of the choke housing is the second stage vacuum box, which pulls the second stage throttle open.
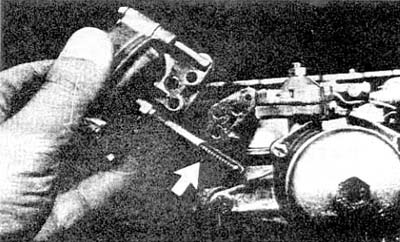
Remove the box from the carburetor body. There is a hole for releasing the ball joint about half way up the brass connecting sleeve.
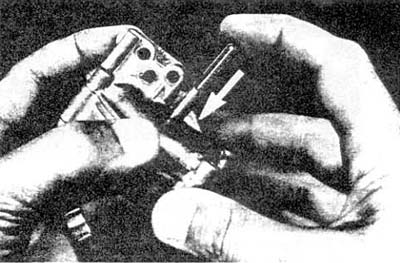
Make sure the diaphragm is not cracked or broken. There�s a quick way to check the condition of the diaphragm without taking it apart.
With the top on, push the rod up into the body of the vacuum box and cover the supply hole with your finger.
The rod should stay in the up position. If it does not, the diaphragm is worn and must be replaced.
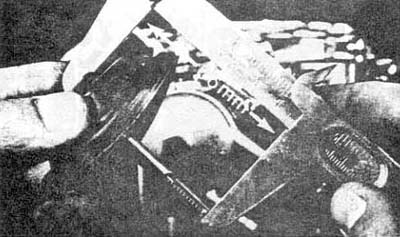
The linkage rod should be 66mm from the support plate to the end of the rod. Adjust the rod if necessary and lock it in place with the jam nut.
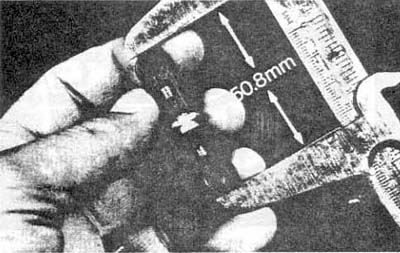
The black plastic intermediate linkage rod should be 50.8 mm from end-to-end, or 40 mm from center-to center.
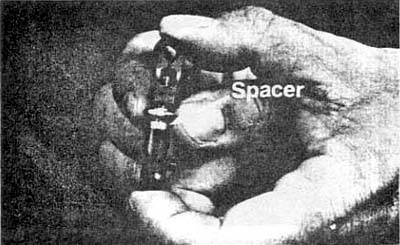
Adjust this distance with the turnbuckle, and snap the rod back on the ball fitting. This is an extremely critical setting, since it is the connection between the Throttle Linkage and the First Stage. The rod should have the metal spacer shown here. If it does not, replace it.
During overhaul, the jets, mixture tubes, valves, and injection mechanism should be removed and thoroughly cleaned. In addition, the float and injection pump may need to be adjusted.
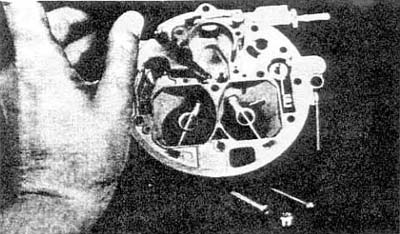
Remove the idle jet, the air correction jets, and the mixture tubes. Make sure they're free of dirt, and the small holes in the jets aren�t clogged. Before you replace them, however, there�s an important note to remember.
First and second stage jets can be accidentally mixed up; and the idle jet can be placed in the second stage.
When re-installing the jets, the smaller jet - the one with the lower number - should always be in the first stage; second stage jets, with higher numbers, are larger than their first stage counterparts.
If jets must be replaced, correct sizes can be found in either the BMW Repair Manual for the model you�re working on, or in the rear of this section, page number 29.
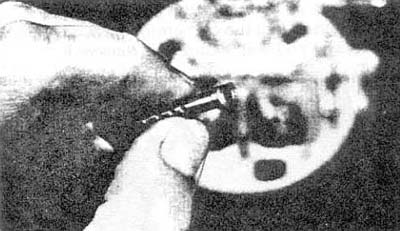
The first stage mixture tube has a flat edge which fits a keyway in the body of the carburetor so it cannot be incorrectly installed.
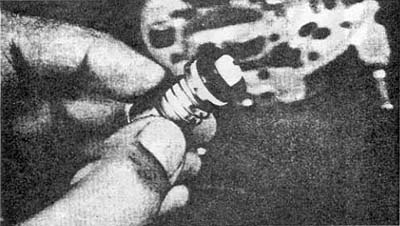
Now, remove the accelerator pump piston, and check the neoprene seal. If the seal is worn, or if it�s the older leather type, replace it The entire piston assembly must be replaced; the seal itself cannot be replaced.

Finally, clean the injection pump nozzle. The fuel discharge nozzle in the first stage must be removed to remove the pump nozzle. It�s pressed into the carburetor body, so a slight "twist and pull" motion will remove it.
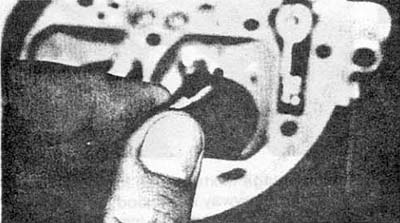
After it�s been cleaned, the tiny hole in the end is free of dirt, press it back into the carburetor housing.
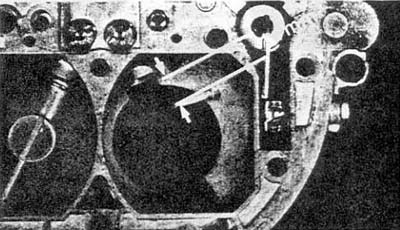
The correct angle for the nozzle is shown above.
The distance from the first stage fuel discharge outlet to the nozzle should be 11 mm.
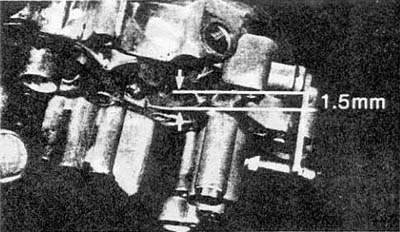
The distance from the nozzle tip to the section parting surface should be 1.5 mm. Injected fuel will now be sprayed down the inside surface of the venturi.
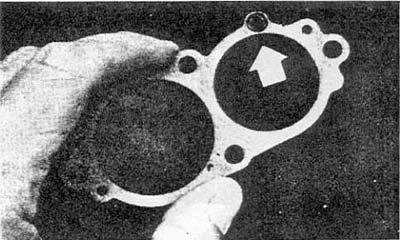
When re-assembling the Base and Float-Bowl Sections, take note of the insulating gasket between the two sections. It should have the "O" ring seal shown here. If it does not, replace the gasket Part numbers are the same.
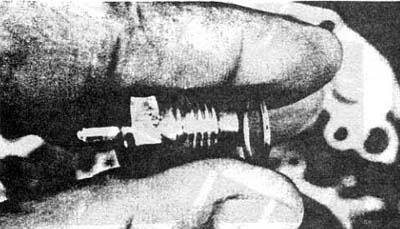
Float level is determined by the thickness of the shim beneath the needle valve. If float level is too high, fuel can dribble into the intake manifold at idle, resulting in excessively high CO readings.
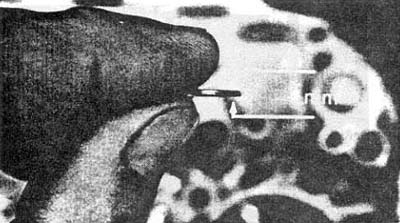
On 2500 and 2800 models, shim thickness should be 1 mm.
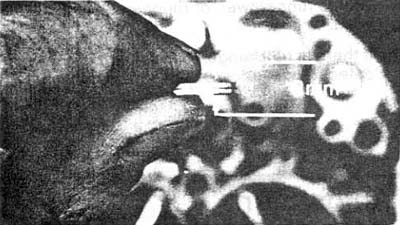
The shim on all 3 litre BMW engines should be 2 mm.
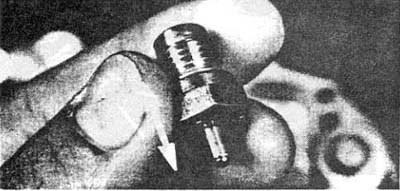
Finally, make sure the needle valve beneath the float is not clogged. It's spring loaded, and should move easily up and return down for a complete seal.
Here�s a note to remember If this valve must be replaced, the new unit must be spring-loaded. The Genuine BMW Replacement Part is, some aftermarket parts are not! Now, re-assemble these sections with the lower portion of the caburetor.
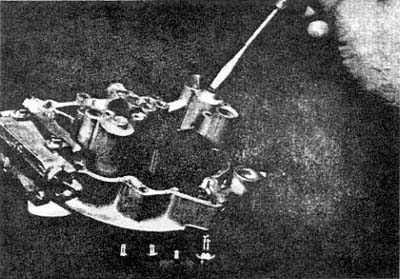
Next, remove, and clean the intermediate jet, the main jets, and the pump suction and pressure valves. Again, make sure the small holes are open.
As before, the main jets can be accidentally mixed up. Make sure the smaller jet - the one with the lower number - is in the first stage.
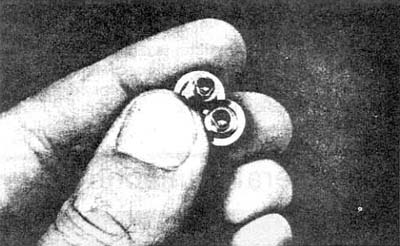
The injection pump pressure and suction valves have steel balls which should move freely. After cleaning, they should "rattle" when shaken.
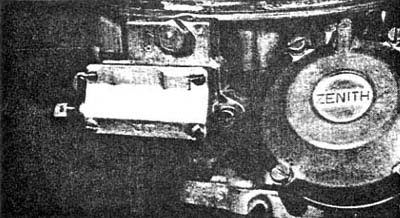
The Thermo-Start Valve is electrically operated and provides extra fuel for enrichment during cold starting for a short period of time.
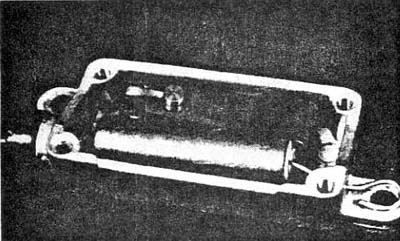
The valve must be cooled to a temperature below 57° Fahrenheit for testing. At that temperature it should remain closed. About a minute after electrical power has been applied to the valve, the bi-metailic should have lifted it off its seat.
If it does not, the resister is defective and the entire unit must be replaced. It cannot be adjusted, since ifs set at the factory under strict climatic conditions.
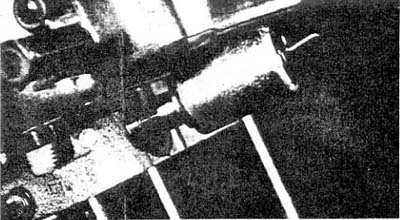
The Shut-Off Valve is an electrically powered solenoid controlled valve that remains open when powered. When the ignition is switched off, the valve closes, interrupting fuel flow to prevent engine run-on.
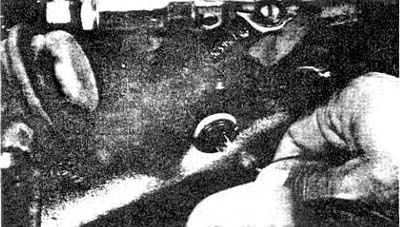
The valve can be checked by disconnecting the lead while the engine is running. If the engine runs slower, or rougher, the valve is good.
If there is no change, the valve is probably defective and should be replaced.
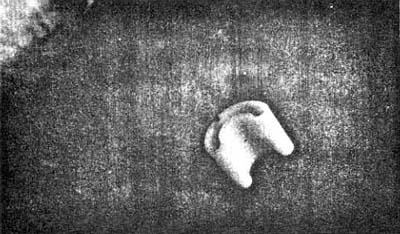
Before replacing the top, injection quantity should be checked with the BMW Test Cup.
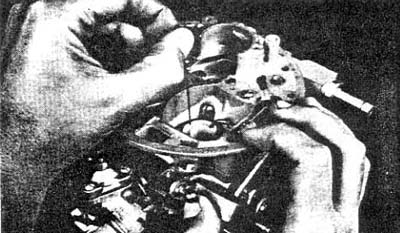
Remove the fuel discharge nozzle. The float bowl should be full of fuel. Insert the test cup in the first stage venturi beneath the nozzle and rotate the linkage to produce injection.
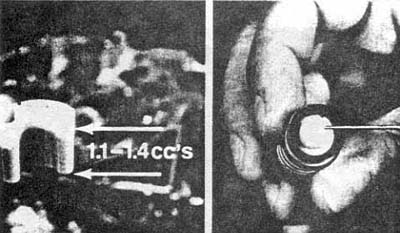
There should be between 1.1 and 1 .4 cc's of fuel in the cup. Injection quantity can be increased by sealing the small hole in the bottom of the piston with a heated pin or paper clip.
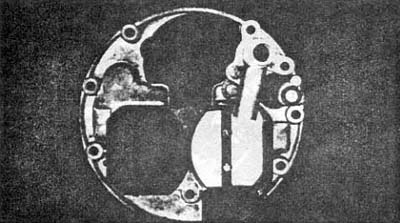
Before re-installing the Top Section, check the Vent Chimney. The carburetors on all 3 litre BMW engines must have a vent chimney like the one shown.
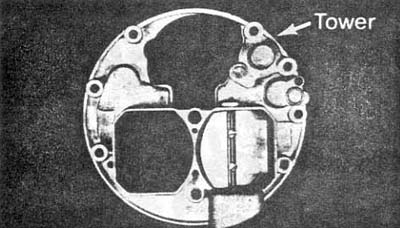
If there is a Tower, like this one, Vent Chimneys must be fitted. The BMW Vent Chimney Modification Kit, part number 13 11 1 259 526 should be used.
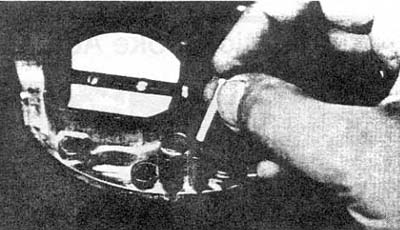
Remove the old vent cover and gasket, and plug the vent hole with the aluminum plug in the kit
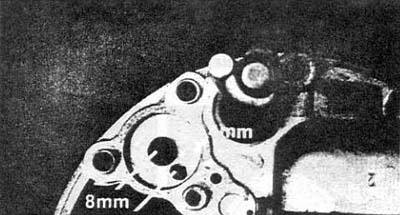
Drill a 4 mm hole 8 mm from the center of the large vent hole.
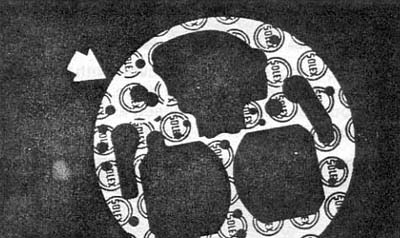
Install the replacement vent chimney gasket, and the replacement top section gasket Note the "Figure-8-Shaped" hole in the new top section gasket.
Install the vent chimney, and replace the top on the carburetor.
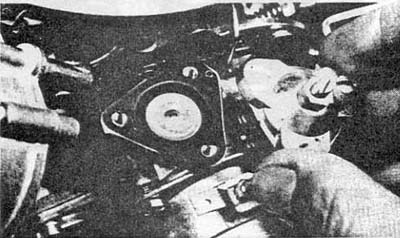
Begin by removing the top cover of the choke pull-down vacuum box and checking the condition of the diaphragm. If it� s cracked or worn, replace it
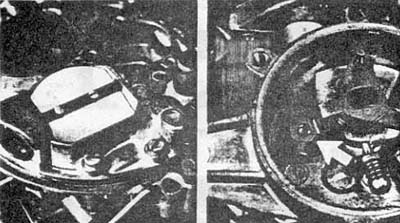
Next, remove the choke cover. With the pull-down plunger all the way down, the choke should be completely closed and the lever should just touch the plunger.
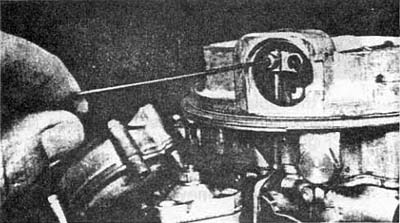
If it does not, adjust the length of the connecting rod with the set screw and snug up the snap ring underneath.
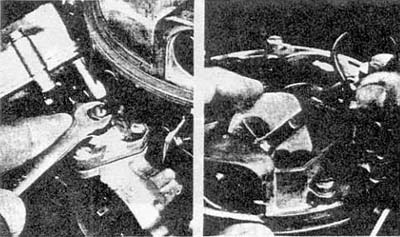
Now, loosen the jam nut of the pull down adjustment screw, and back off the screw. Insert a 3 mm tool between the bottom of the choke
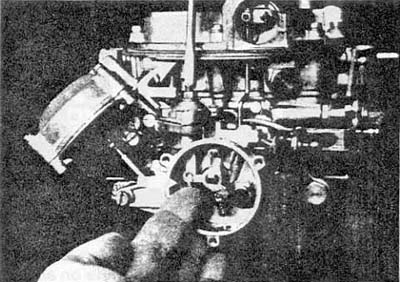
the connecting lever, and turn the adjusting screw in until it just touches the top of the plunger. Tighten the lock nut.
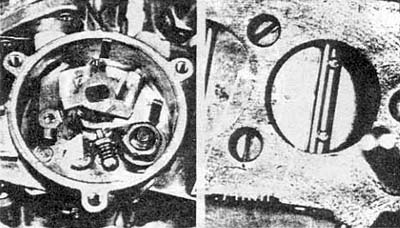
Now, set the fast idle adjustment screw. The basic setting is with the screw on the highest notch of the fast-idle cam, the first stage throttle plate should be open .7 mm.
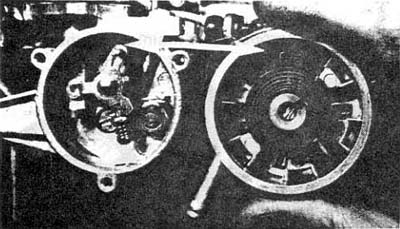
When replacing the choke cover, do not forget to fit the pin on the choke connecting lever into the opening on the bi-metallic spring, and align the marks on the covers. Now, mount the carburetor on the engine.
Note: dwell and timing must be correct and the engine must be at its full operating temperature.
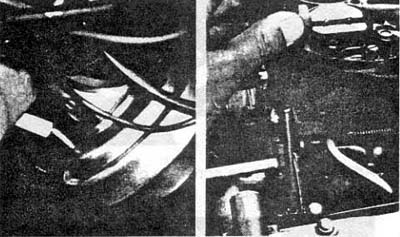
Remove the air cleaner housing. Disconnect the vacuum advance and retard lines. Turn the screw on the connecting linkage between the two carburetors in to bring RPM�s up to 1700.
Timing should be 22° before Top Dead Center. Now, drop RPM's back to normal (900 RPM's), and reconnect the vacuum lines.
There are two BMW Special Tools used for carburetor synchronization: a secondary breather pipe and a kit which contains synchronizing cups and a meter.
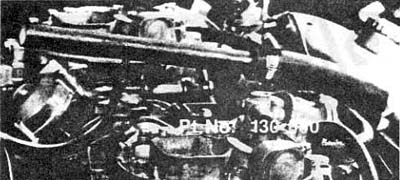
Install the breather on the rocker cover and connect the vacuum lines.
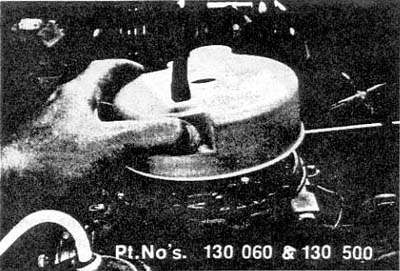
Install the synchronizing cups on each carburetor.
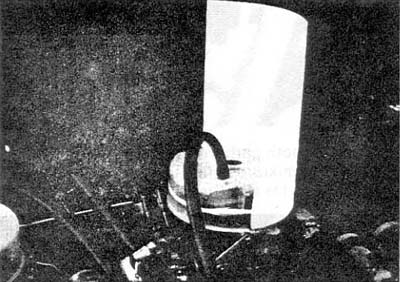
Note: Place a cardboard shield around the front cup so air flow is not affected by the fan.
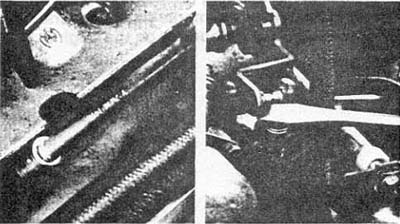
Remove the CO plugs from the manifold, and pop off the connecting linkage between the two carburetors. It's alongside the rear carburetor.
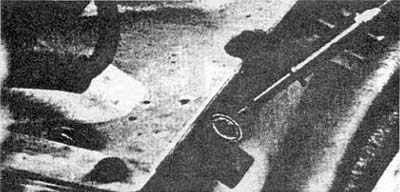
Now insert the CO Probe into either the front or rear manifold hole - whichever you choose.
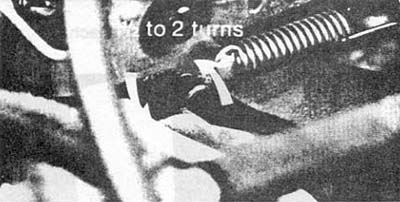
If one, or both carburetors have been rebuilt, run in the mixture screw until it bottoms, then back it out 1� to 2 turns.
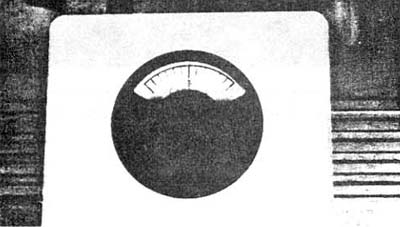
The procedure is to adjust RPM�s and the balance between the two carburetors so the needle is zeroed, while maintaining the correct CO value.
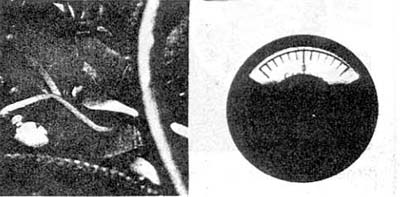
Adjust the throttle screw on each carburetor to obtain 900-1000 RPM's while keeping the needle on the meter zeroed.
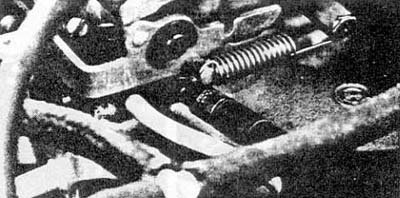
Adjust the mixture screw to get the proper CO value for that model.
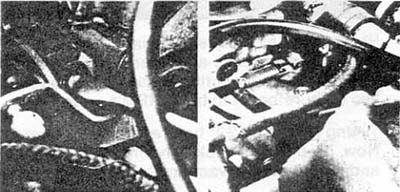
After adjusting CO. it may be necessary to readjust idle speed. Re-check CO, and re-adjust that if necessary. The final check should always be CO.
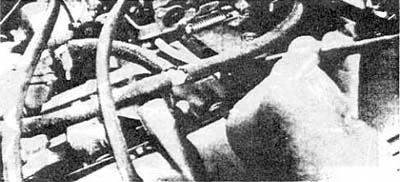
Remember, turning in the mixture screw leans out the mixture and lowers CO; turning it out richens the mixture and consequently raises CO.
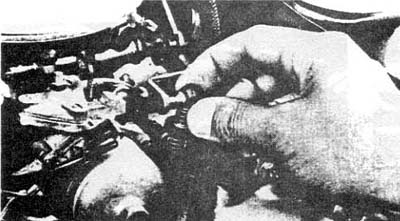
Once the desired readings have been obtained from both carburetors, re-attach the linkage between the two.
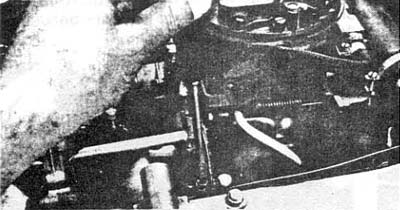
Raise RPM's to 1700 with the screw on the connecting linkage and check the meter.
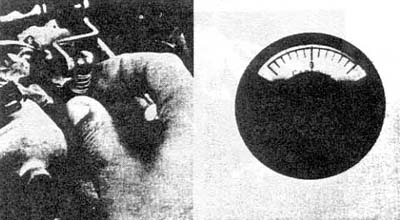
Adjust the knurled nut on the turnbuckle to zero the meter.
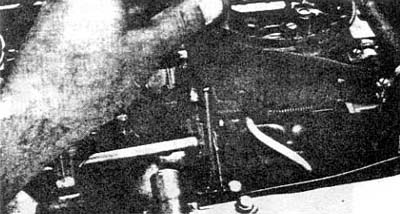
Back off the screw to allow engine speed to return to idle. Make sure the screw is not touching the throttle linkage; it should never be used to set idle speed.
The adjustment for fast idle should be done with the flow meter disconnected, the carburetors correctly synchronized, and the engine up to full operating temperature.
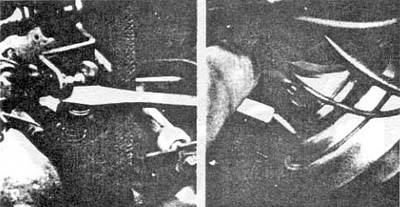
Turn off the engine and disconnect the linkage on each carburetor. Disconnect both advance and retard vacuum lines on the distributor and plug them up.
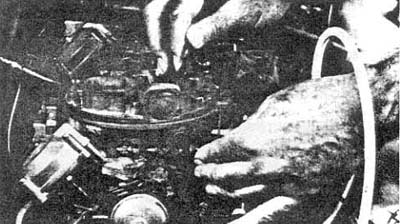
On one or the other carburetor, hold the throttle linkage open while setting the choke flap to an opening of 3 mm. Carefully close the throttle and release the choke flap. This puts the fast-idle adjustment screw on the second step of the fast-idle cam.
Without touching the accelerator, start the engine. It should idle at 1600 to 1700 RPM's. If it does not, it must be adjusted with the screw inside the choke housing.
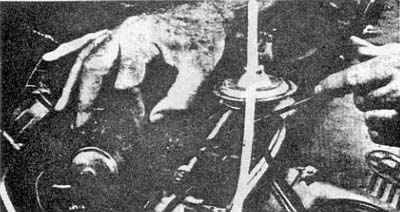
Stop the engine, turn the linkage to full throttle, and adjust the screw through the small hole in the housing. One full turn of the screw equals approximately 300 RPMS's.
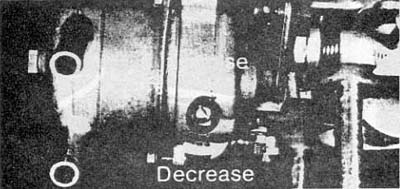
By turning the screw to the right. RPM�s increase; to the left, they decrease.
After making the adjustment, reset the carburetor to fast idle and re-check the speed.
Repeat this procedure for the second carburetor.
Now, with both carburetors on the second step of the first idle cam, start the engine. If adjustments are correct, RPM's should. not exceed 2200.
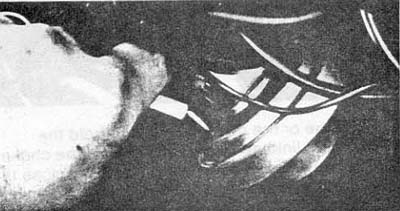
Reconnect the vacuum retard line, and RPM�s should drop between 200 and 300. There should be no change when the advance line is reconnected.
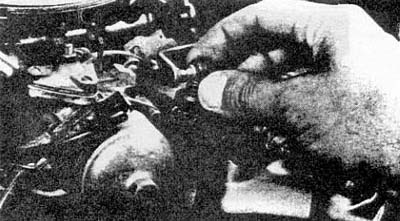
Reconnect the linkage between the carburetors and release the fast idle cam by stepping once on the accelerator. RPM's should now drop back to normal - between 900 and 1000.
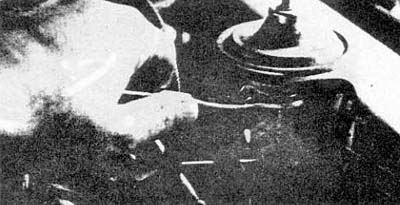
Finally set the Dash pot linkage with the vacuum line disconnected. Adjust the nut so the arm holds RPM�s at 1500 on deceleration.
Prior to the introduction of the 3 litre engine, there were no individual CO plugs on the manifold. CO readings were taken only at the tailpipe.
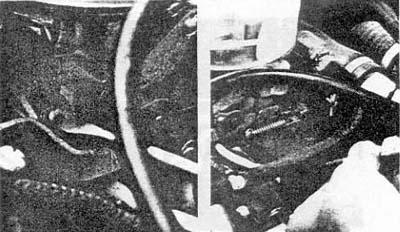
CO adjustments are made by first adjusting each carburetor to Best Idle.
Then turn in each mixture screw the same number of turns to obtain specified CO.
But in '74 we made a few changes. The biggest difference was the addition of a second idle circuit and a modified Cold-Start System, sealed Throttle Stop Screws, and additional Jets.
Since throttle plate stop screws were correctly set at the factory, and are not intended to be adjusted, there is a special procedure for resetting that screw, plus slightly different synchronizing procedures using the idle by-pass screw and the mixture screw, rather than the stop screw.
For resetting the throttle stop screw, assuming the carburetors cannot by synchronized in the normal manner, the engine must be at full operating temperature and the air cleaner must be off.
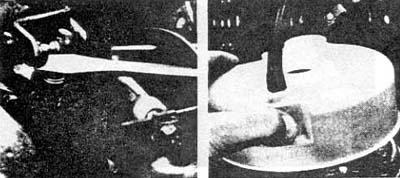
Remove the vacuum retard line from the distributor and plug it up. Remove the linkage from the carburetors, and install the test cups and meter.
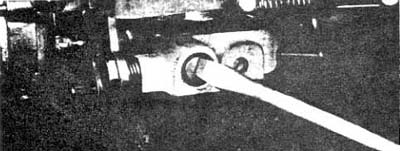
Close the mixture by-pass screws - run them in until they bottom.
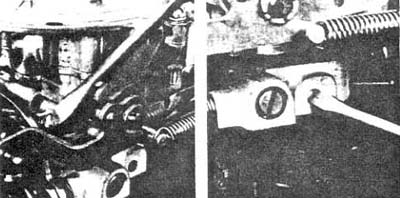
Now, synchronize both carburetors with the idle adjustment or stop, screws to 900 RPM�s, and bring CO to 3 per cent with the mixture screws.
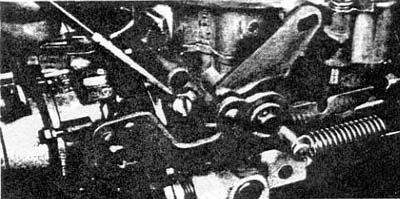
Once the desired balance has been obtained, lock the idle stop screws with plastic caps or a paint spot.
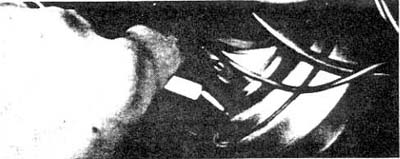
Reconnect the vacuum hose. RPM�s will drop to approximately 700.
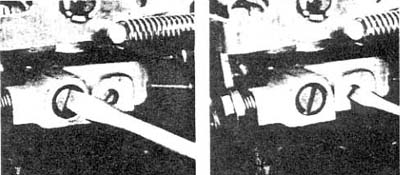
Now, repeat the synchronizing procedure using the idle by-pass screws and the mixture screws. This procedure is basically the same as for earlier carburetor models.
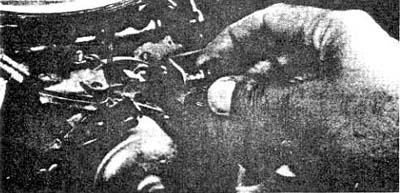
Reconnect the linkage, and check synchronization at fast idle. If everything is OK, replace the air cleaner.
For normal synchronization, procedures are very similar to earlier models.
The engine must be at normal operating temperatures, and the air cleaners must be removed.
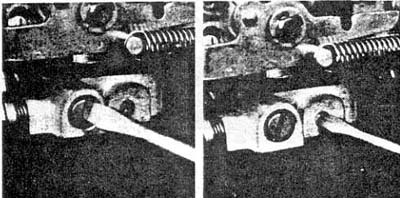
With the idle by-pass crews, adjust RPM�s to 900 to 1000, and with the mixture screw, adjust CO to a maximum of 2 per cent As before adjust the two screws on each carburetor together until the desired readings are obtained.
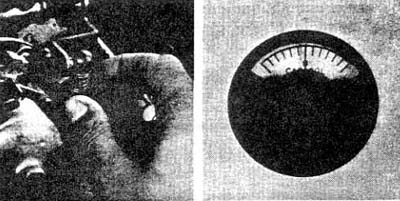
Now, reconnect the linkage rod and adjust the knurled nut until the meter is zeroed.
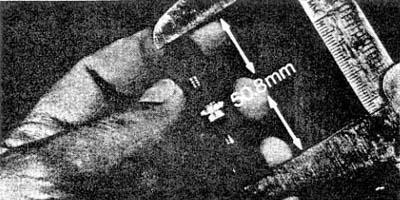
If, after the linkage rod had been reconnected, it is difficult to obtain the correct balance, check the length of the short plastic rods that connect the first and second stages. They should be 50.8 mm from end-to-end, or 40 mm from center-to-center.