Background: I want to build a wood rimmed steering wheel. But I want to build it using the stock csi sport wheel frame and with the same wood I have on my dashboard (etimoe).
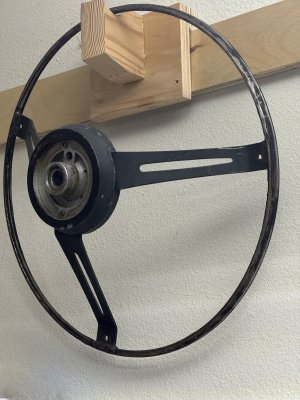
I want to do it so the wood grain follows the circle of the wheel like a proper Nardi would. I thought about steam bending but there are several issues with that, including how do you join the two ends cleanly in a way that the whole thing will not split open at some point.
So, instead of starting with solid wood, I would like to use bent lamination, ie wrapping a continuous strip of thin veneer of the same etimoe I used on my dashboard around the steel frame to build the outer thickness. Maybe 5mm or so thick.
Once that is done, using the same technique, I will build inner layers. Then at the end I would sand it all down to the proper rim thickness and shape. If this works as planned (and I realize it's a big "if"), it should make a nice match between the steering wheel and the rest of the car woodwork.
The tool setup I need: I have a steering wheel column to which I can secure the wheel (on the left in this photo)
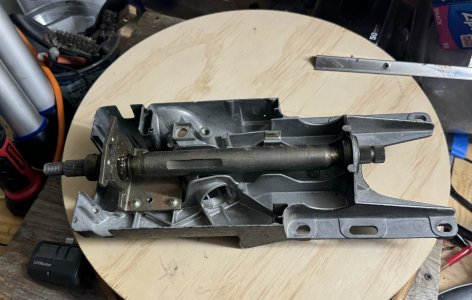
I would like to setup a small electric motor that will spin this column (by grabbing the spindle on the right in this photo) which will then spin the wheel so it can be sanded. Much like you would do in wood turning. I imagine attaching the whole contraption to a base, securing the motor next to the column and using a belt of some sort to grab the spindle on the right. This motor would need to have variable speed for ideal control.
There are plenty of motors available on eBay but they are generally too powerful and fairly expensive ($150+). And then there is the issue of finding a belt that can fit on that motor on one side and that can grab the grooved spindle on the other.
I know several here have built similarly crazy contraptions ... Any thoughts on how to bring this to reality?
Thank you very much
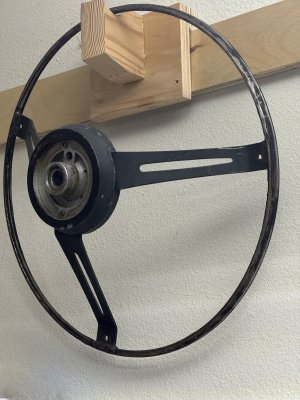
I want to do it so the wood grain follows the circle of the wheel like a proper Nardi would. I thought about steam bending but there are several issues with that, including how do you join the two ends cleanly in a way that the whole thing will not split open at some point.
So, instead of starting with solid wood, I would like to use bent lamination, ie wrapping a continuous strip of thin veneer of the same etimoe I used on my dashboard around the steel frame to build the outer thickness. Maybe 5mm or so thick.
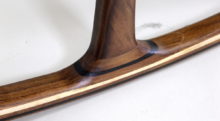
Once that is done, using the same technique, I will build inner layers. Then at the end I would sand it all down to the proper rim thickness and shape. If this works as planned (and I realize it's a big "if"), it should make a nice match between the steering wheel and the rest of the car woodwork.
The tool setup I need: I have a steering wheel column to which I can secure the wheel (on the left in this photo)
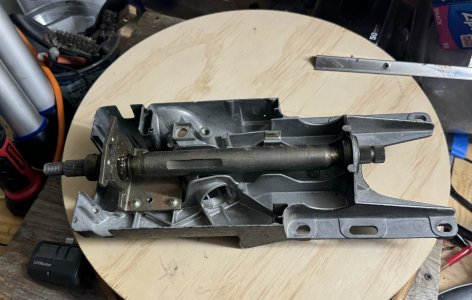
I would like to setup a small electric motor that will spin this column (by grabbing the spindle on the right in this photo) which will then spin the wheel so it can be sanded. Much like you would do in wood turning. I imagine attaching the whole contraption to a base, securing the motor next to the column and using a belt of some sort to grab the spindle on the right. This motor would need to have variable speed for ideal control.
There are plenty of motors available on eBay but they are generally too powerful and fairly expensive ($150+). And then there is the issue of finding a belt that can fit on that motor on one side and that can grab the grooved spindle on the other.
I know several here have built similarly crazy contraptions ... Any thoughts on how to bring this to reality?
Thank you very much
Last edited: