goodolarchie
Member
- Messages
- 25
- Reaction score
- 0
This weekend is all about dealing with the floor. All four pans have rust through, though driver side is the worst. Here is some recon (let me know if these images are too large, they should fit fine on anything larger than 1024):
(Yes that is speaker wire from some hack job done by PO
And now for the patching:
Tacked real snug by using a jack below.
(Was this fiberglass filler beneath the undercarriage coating? Lots of whispy fiberous crap came off..)
Then the tacks were stitched together with lap welds
First one done, passed the dye penetrant inspection.
There is about 1/2" overlapped underneath that needs to be seam sealed and POR coated.
Now on to the BAD metal!
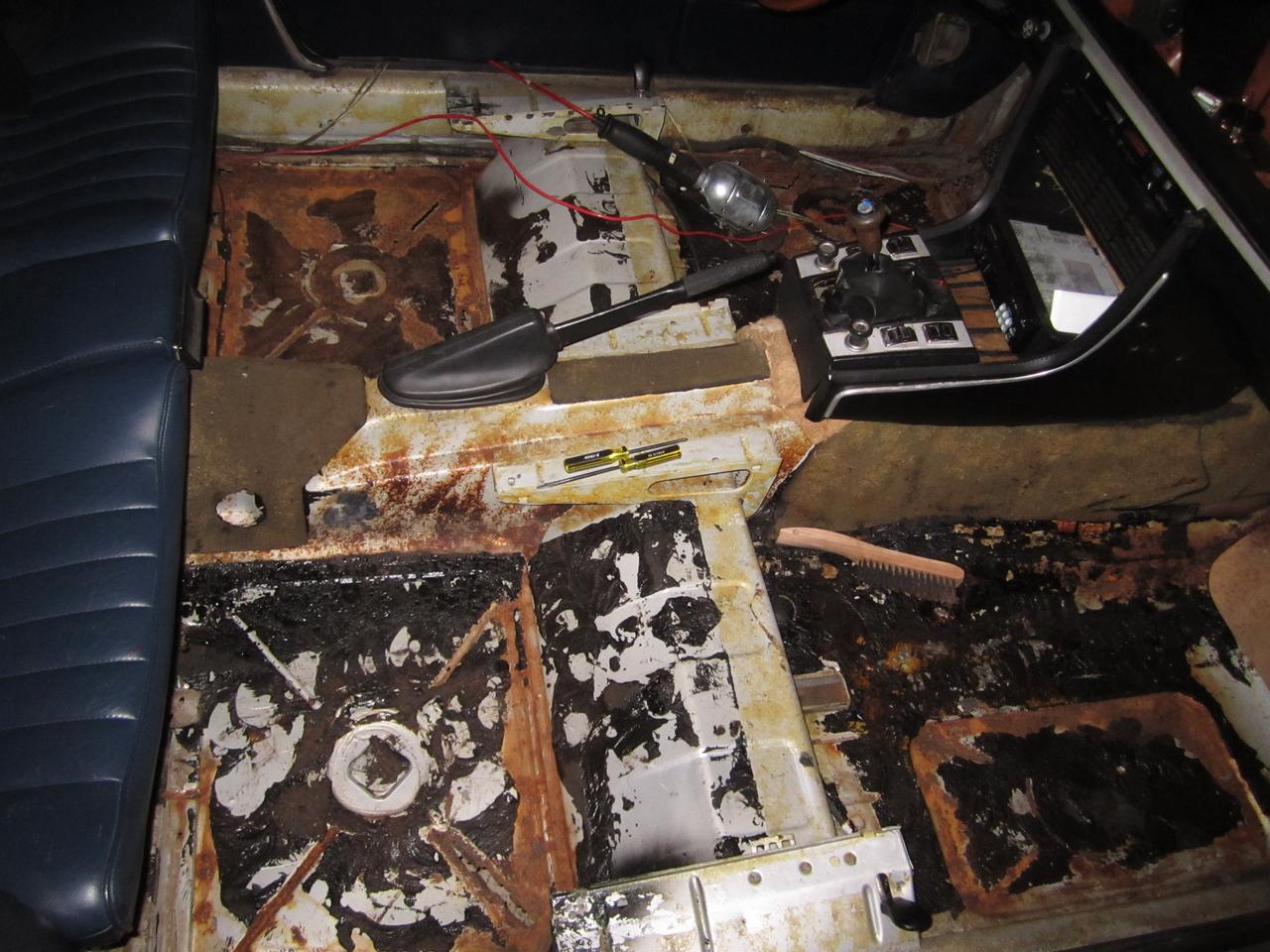
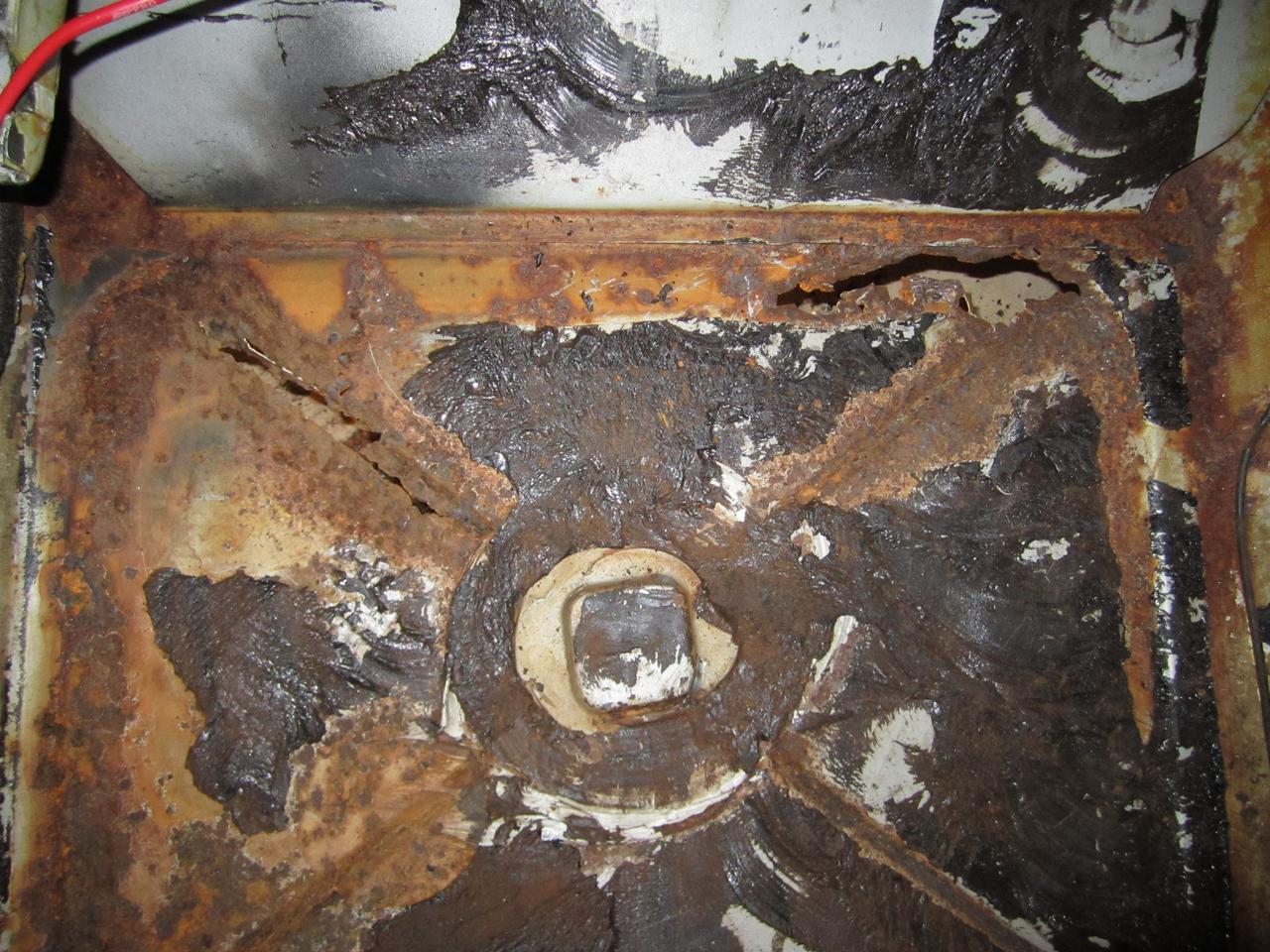
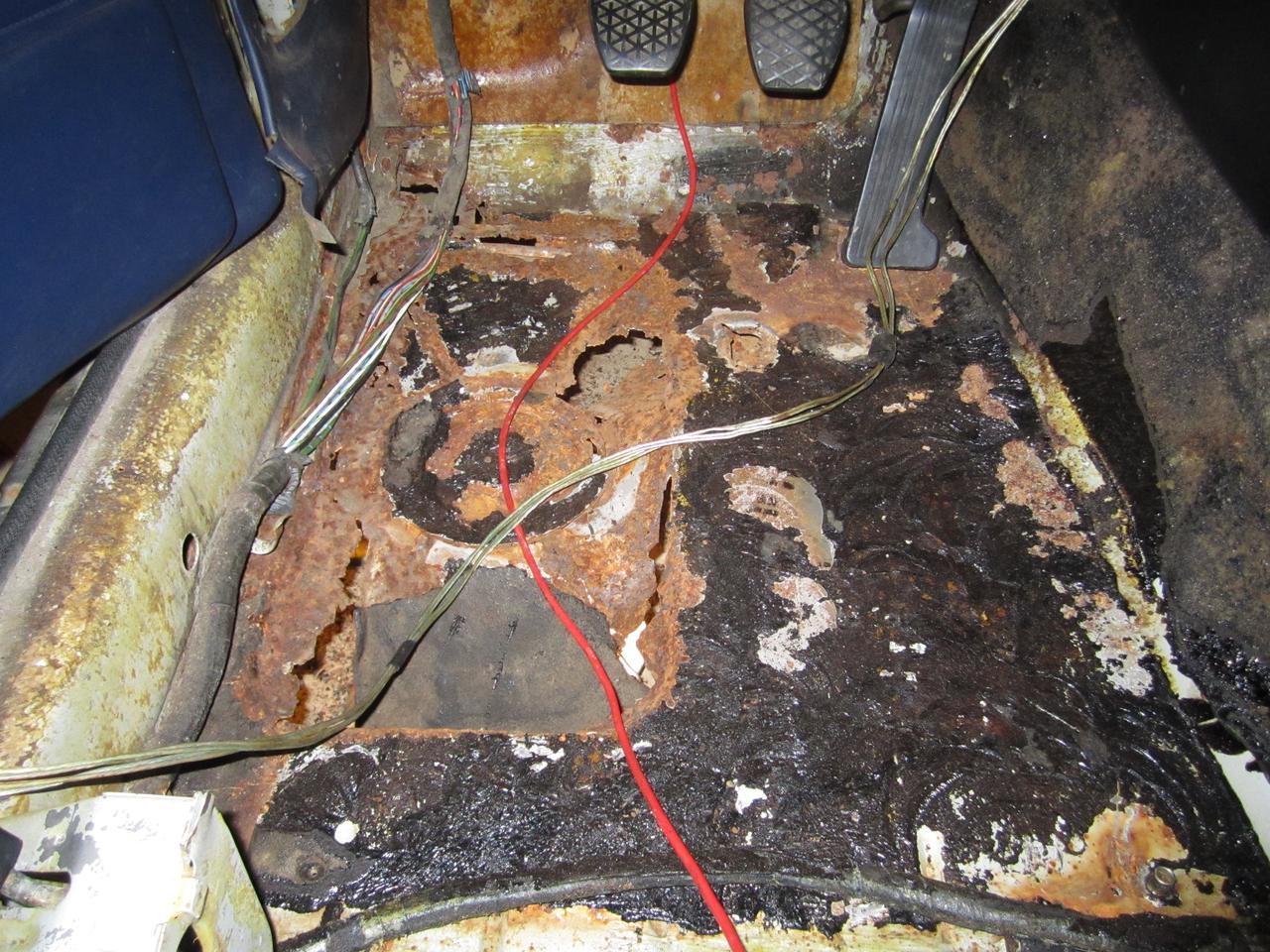
(Yes that is speaker wire from some hack job done by PO
And now for the patching:
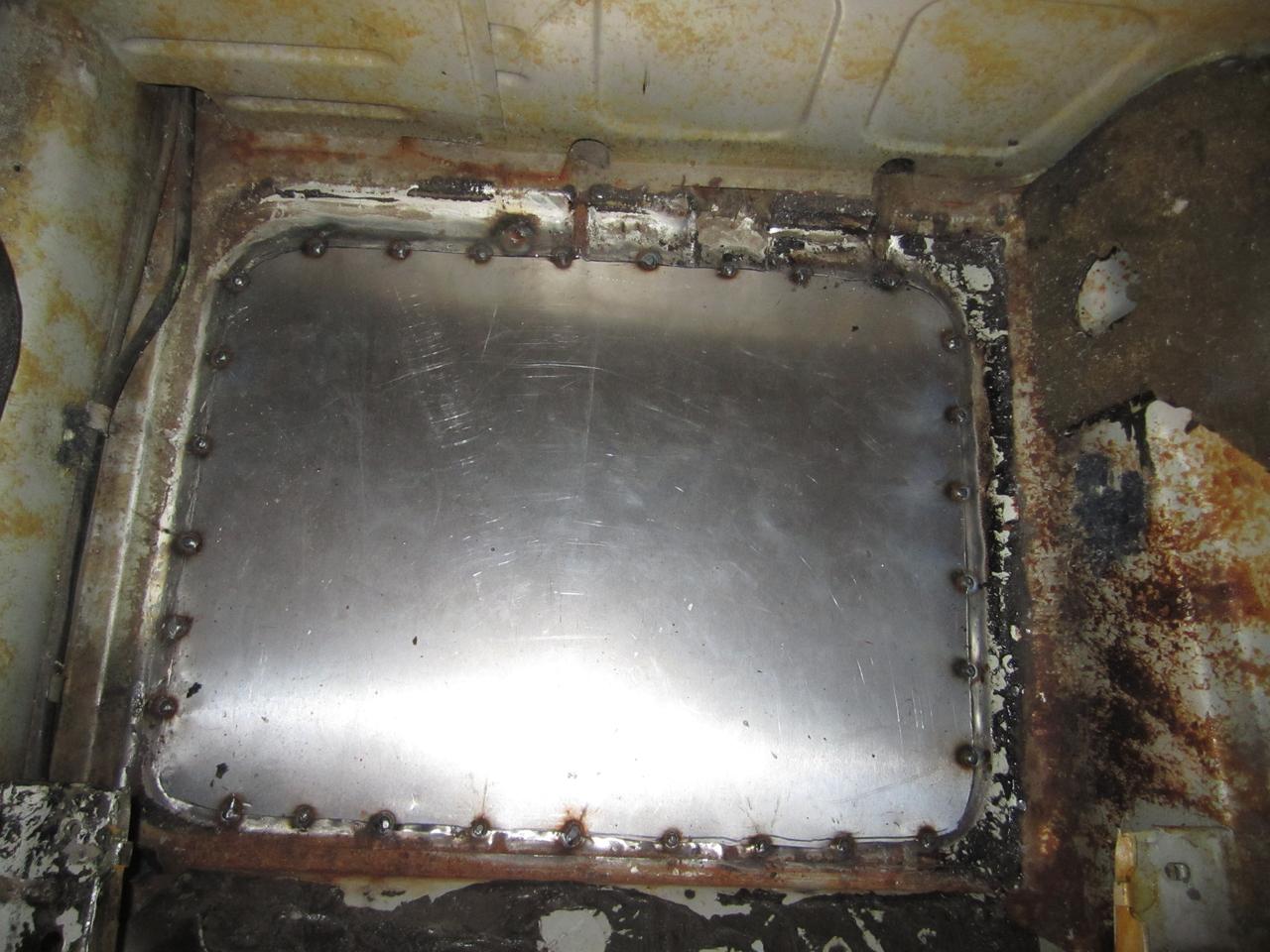
Tacked real snug by using a jack below.
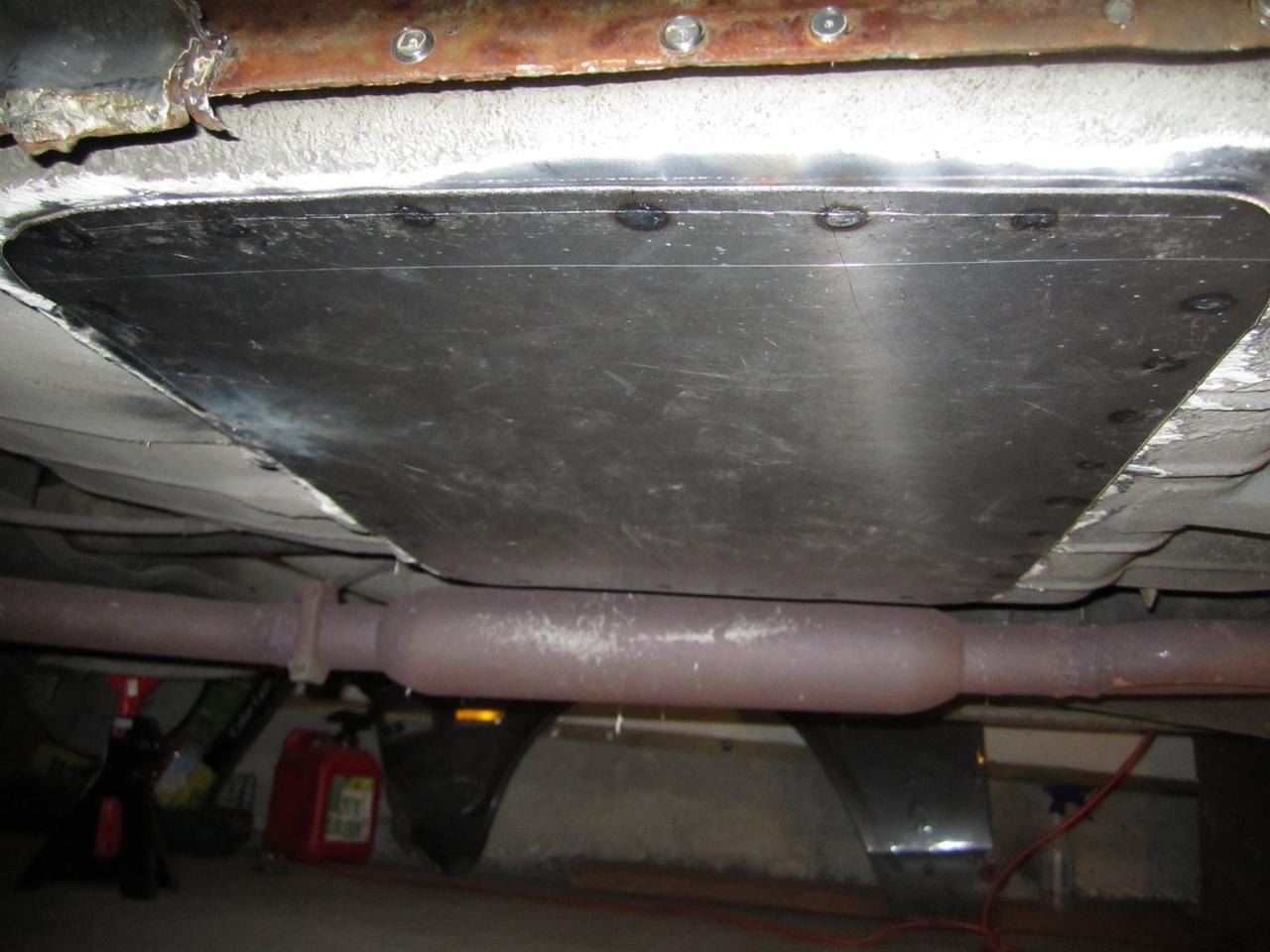
(Was this fiberglass filler beneath the undercarriage coating? Lots of whispy fiberous crap came off..)
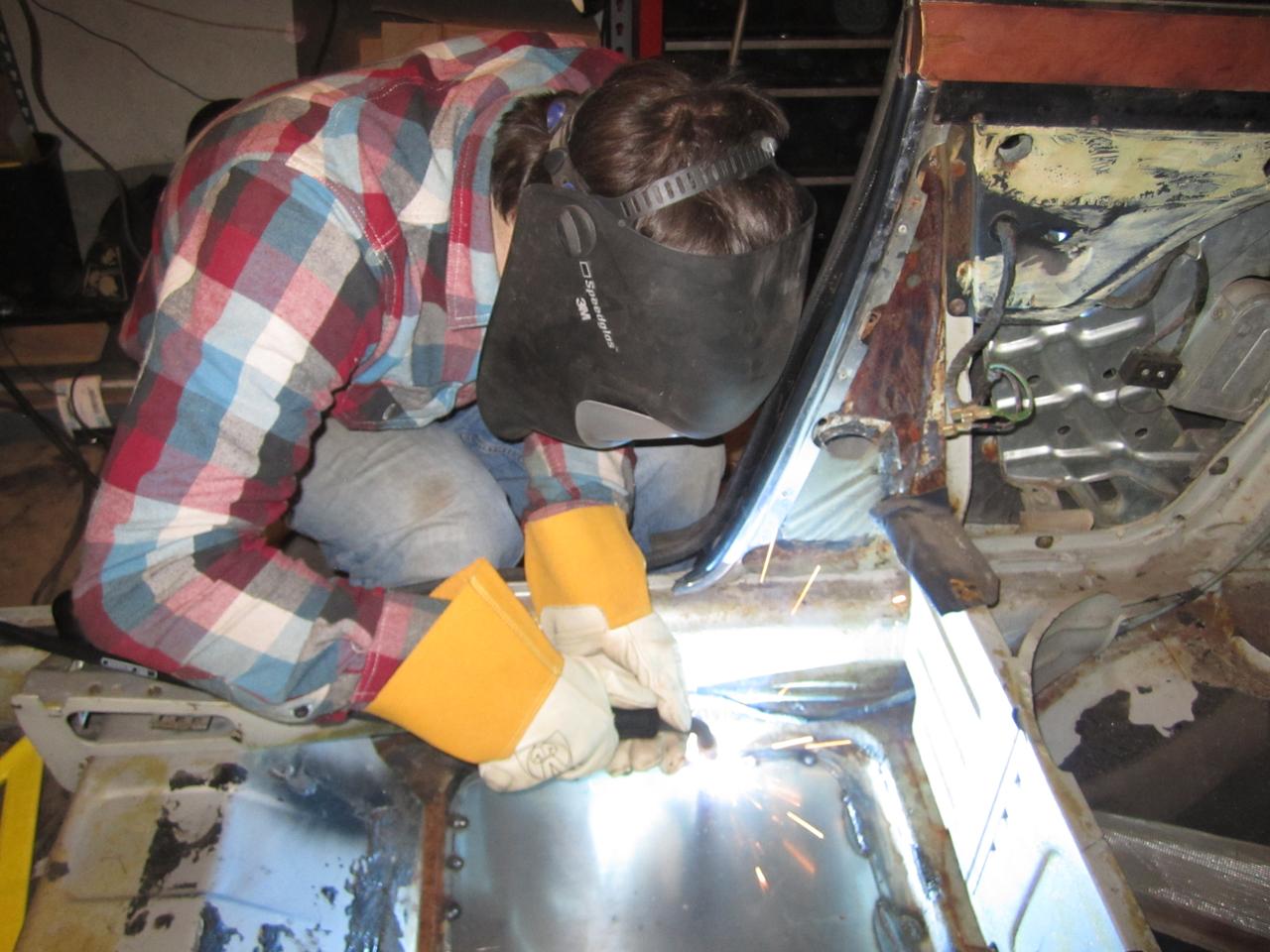
Then the tacks were stitched together with lap welds
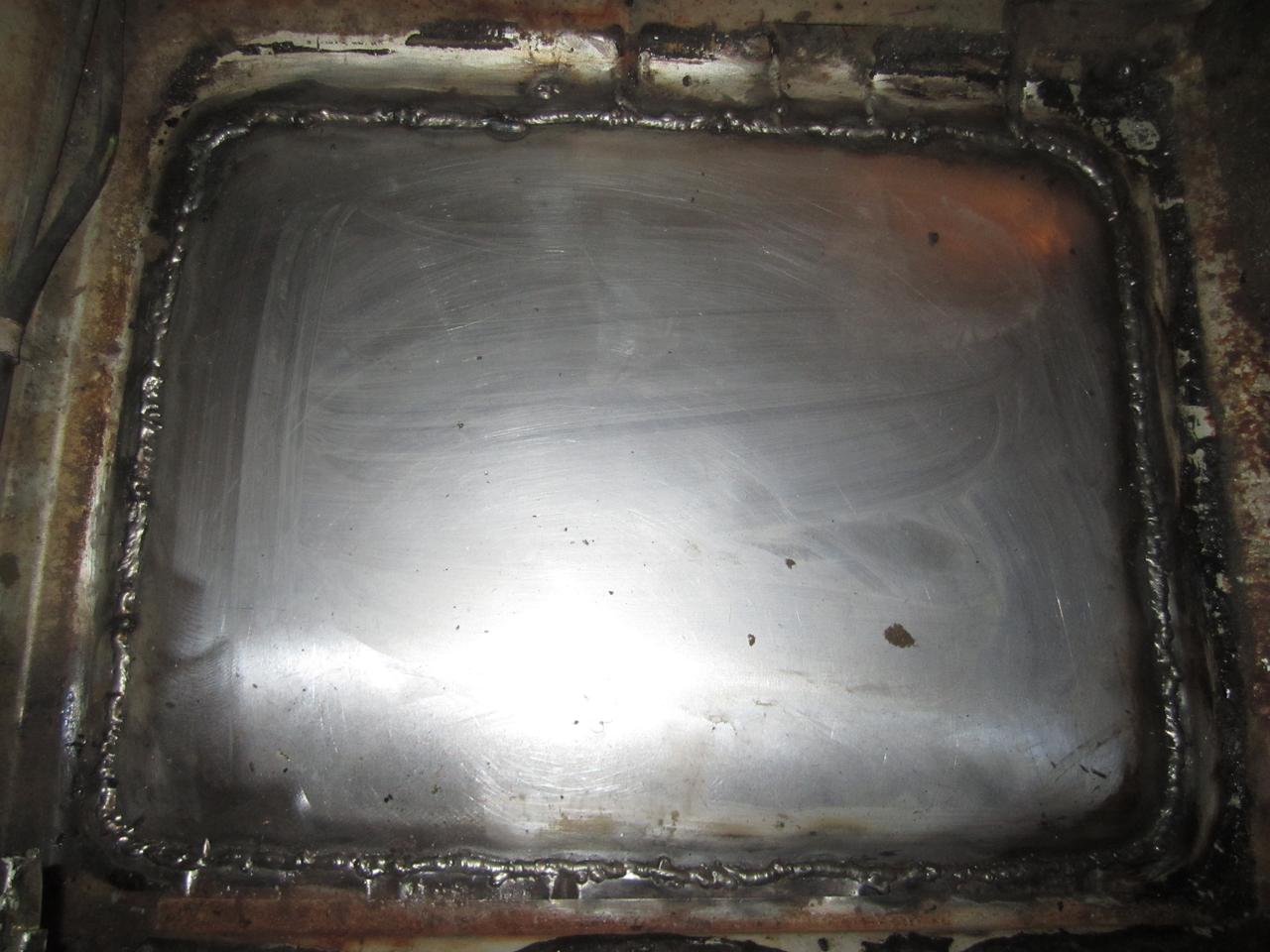
First one done, passed the dye penetrant inspection.
There is about 1/2" overlapped underneath that needs to be seam sealed and POR coated.
Now on to the BAD metal!