BMW workshop manual . . . all say they are one time only. They cost $1.40 each and I am cautious about rotating parts.
With respect, where in theE9 shop manual is it recommended that Giubo or Jurid Joint fasteners be replaced after one use?
http://www.e9-driven.com/Public/Library/BMW-E9-Manual/pages/en/26115410.html#refertoc
An answer about the nuts of the guibo
I wouldn't dare to use nuts with a plastic ring ('Nyloc' as there called in Europe) as I think the radiant heat from the exhaust may well bake the plastic, losing the friction function it has. For the same reason I wouldn't trust Loctite, as that starts to lose function around 200 degrees Celsius (400 Fahrenheit), and completely disintegrates around 250 degrees Celsius (485 Fahrenheit).
You raise an interesting point regarding nyloc nut heat exposure. However, if this was a serious concern, the factory would have issued a technical service bulletin advising against using nyloc fasteners for this purpose - or at least recommend very frequent inspections. (If you are concerned about the nuts' structural integrity and longevity what about the bolts? Look at link below depicting a worn bolt shank.)
It is prudent, whenever a critical fastener's condition is in doubt, to replace it. Still, I can't recall hearing about any drive shaft's dropping or detaching from the transmission specifically due to a fastener failure. This doesn't mean it hasn't happened, but I can't recall hearing about it. (Discussion at bottom describes fastener wear or failure - but not a catastrophic drive shaft detachment.
There are obviously exceptions, but typically, the weakest link in the drive line is the fat rubber jurid joint. When the joint is in bad shape there is generally fair warning due to significant vibration. (Of course a few may look perfect until they are removed.) Next, those six 12M bolts should be properly torqued (see chart below) in which case, when it comes to torsional stresses, the nylon portion of the nut is relatively insignificant as compared with the metal portion of the nut. The nylon's function is mainly to arrest vibration and its clamping force is de minimus.
IIRC, a rule of thumb when employing nyloc nuts is to measure the torsional resistance when the nut is "free-threaded" on the bolt or screw. That resistance, might add up to a lb./ft. or two - on a large fastener such as a control arm bolt. And that additional resistance is added to the overall torque load so that the combination of the two torque measurements equal the recommended torque. Given the generally wide latitude of torque recommendations, the math is not that critical. Aircraft applications generally require more care with arithmetic.
Some commentary regarding nyloc reuse seems appropriate:
Threaded fasteners for critical aerospace applications usually require two forms of locking function, one being the thread friction from installed pre-load, and the other usually being the thread friction from a locking element. QA procedures usually require that both the running torque and final torque are measured, and witnessed/recorded by an inspector.
With small diameter self-locking threaded fasteners (ie. .25 inch and smaller), it is important to ensure that the running torque of brand new locknuts or inserts falls within an upper and lower range. With small diameter all-metal locknuts or inserts it is very difficult to accurately control the running torque, and a percentage of brand new parts may greatly exceed the procurement standard limits. High running torque can result in excessive shear stress in the bolt/stud after installation. I've personally experienced situations where we had to trash around 10% of brand new 10-32 MS21043 all-metal locknuts because the running torque was too high. It was very tedious to check the running torque of dozens of locknuts for each assembly, but due to the relatively large number of brand new locknuts we rejected it was obviously worthwhile.http://www.eng-tips.com/viewthread.cfm?qid=356115
Even if one or several Jurid joint nuts and bolts were to become loose, it is unlikely that the joint would be disconnected from either the transmission or the drive shaft - without ample warning. First, respecting the original unreinforced rubber donut, recall that it is under tension when it is first installed. Remember the metal band? Thus, it tends to hold the bolts in place when the band is removed. ( Yes, the tension is probably released with centrifugal force created by the spinning shaft.) Setting aside the likely vibration that should alert most drivers to a serious problem, there would likely be serious noise if the bolts started to travel from their normal position and contact any stationary object, e.g., a transmission boss or similar protrusion fore or aft or the joint. For obvious reasons - any and all contact between a moving bolt and a stationary object is to be avoided. Yet, practically speaking, unwanted bolt travel generally reveals itself very quickly, but not so quickly that a prudent driver wouldn't pull to the side of the road. And bolt travel would likely be very incremental since there are no obvious forces, e.g., a hammer and punch, directing it/them. I mention this also having noticed a few transmissions with "interesting" contact marks that likely came from a loose Jurid Joint bolt. Fortunately, in each case, the damage appeared more cosmetic than structural.
Note spelling "Giubo."
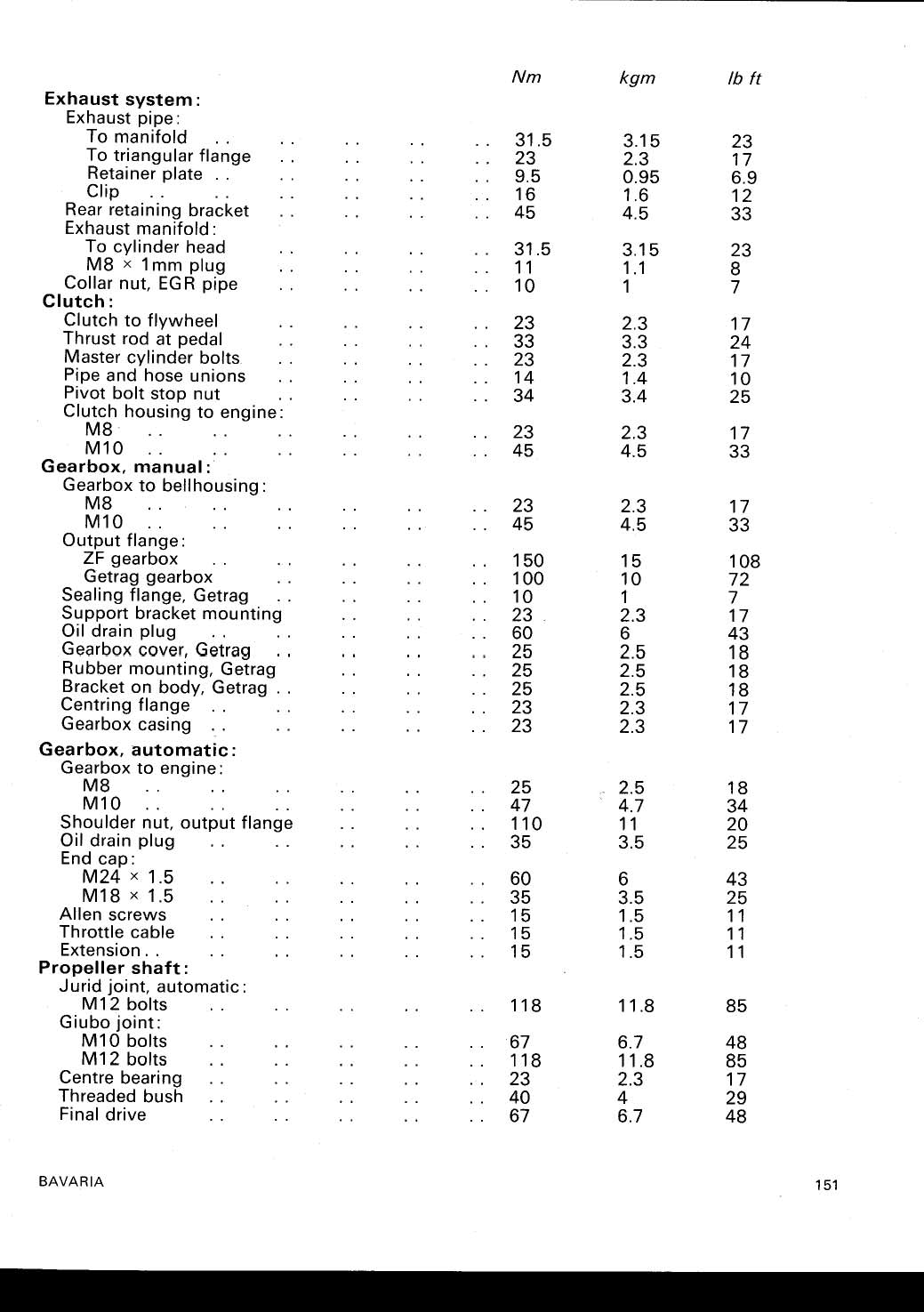
For illustration purposes.
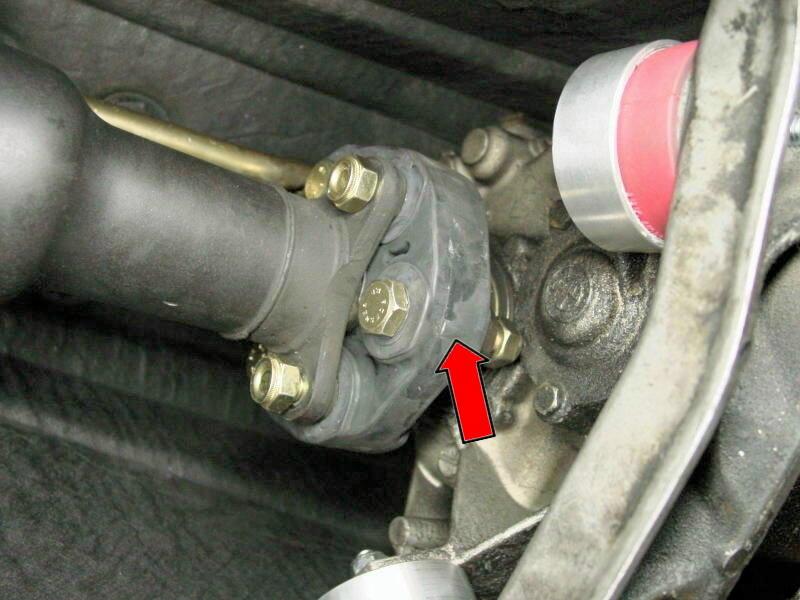
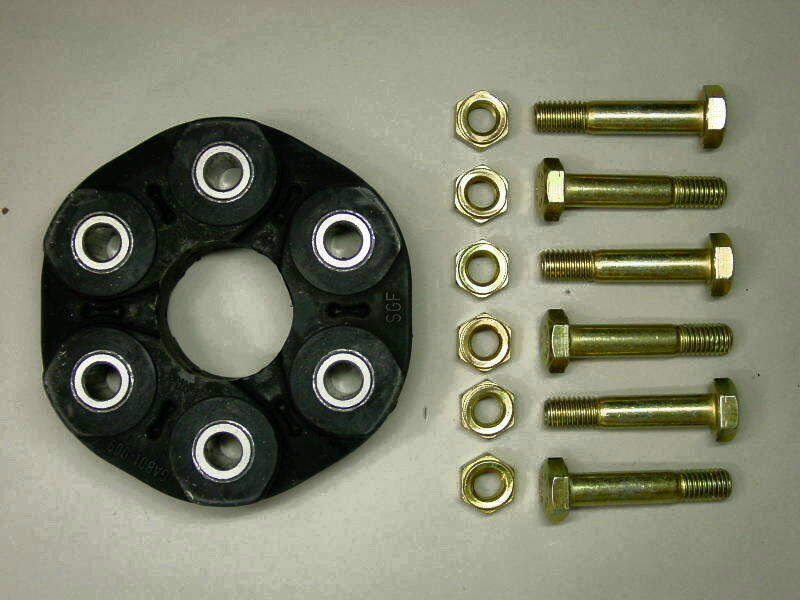
A discussion regarding why Jurid Joint fasteners should be inspected. http://www.bimmerforums.com/forum/showthread.php?2069040-WHY-you-need-to-be-sure-the-guibo-nuts-bolts-are-tight Cause or effect? Chicken or Egg? Please note that nut and bolt failure may not have had anything to do with using nyloc nuts or the fasteners themselves. Could problem have arisen by merely leaving bolt loose (finger tight) or other worn/defective components?

Last edited: