decoupe
(deceased)
I did my first performance driving session last June using a friends hopped up WRX STi - which was an amazing car to start with but whose limits are so far beyond mine that I need to start over and grow into the sport. To that end I’m going to continue to modify my ’73 CS into a more trackable street car (as opposed to streetable track car) with continued comfort on road trips also being maintained.
I dropped the car off at the home of a welding instructor (Chris McQuay) at a community collage that runs a custom welding and fabrication business –Unobtainium Welding http://www.higherarcing.org/ as a side venture (soon to be full time). My list of requirements included seam welding wherever possible (I did the prep grinding for most of it), main hoop and back legs to follow the line of the windows, one removable diagonal bar in the main hoop, chassis stiffening and repair of some nasty work done when the sunroof was added in the mid 80’s. The ability to leave the rear functional for gear beyond what the trunk could carry on multi day road trips was paramount and had a major influence on design (apparently) and cost (definitely). In addition, I removed all four windows for a thorough cleaning and de-gunking (grease becomes wax after 3 decades) – motors were all fine.
First order of business was gutting of the interior and elimination of the sunroof, which was never something I looked for in any vehicle I’ve owned, though it was fully functional. It’s a hole in the roof, right? It’s Canada, not SO CAL, eh? Motor was in the trunk
and in order to get the cable drive to it, the passenger C pillar was split from as to teakettle with two little metal straps riveted to the sheet metal for repair. That and a couple other hacks would be repaired along with the seam welding (as per Coupeking).
One used sunroof.
One hole in roof.
Additional plates were added on the wheel arch, driveshaft hump and the seat bulkhead at the rear quarter window flare.
Light gauge plate was fabricated into structural boxes for the main hoop to weld onto that resist punching through the floor and allow access to the 360 joint to be welded. Brace tubes ran from these boxes to the transmission tunnel strengthen the chassis.
.
Each of the boxes has a sleeve in which to run all the wiring to rear lights, fuel pump, amps and speakers and batteries.
The main hoop has a removable diagonal brace from top driver corner to bottom passenger plus a plate gusset in each of the upper corners. An anchor point was added outboard on both sides of the main hoop for the top swivel bracket for a reproduction 2002 (Coupeking again) 3 point seatbelts.
The Recaro SRD seats in the car are not compatible with a four point harness and I’m not willing to give the blissful comfort and support they offer. If I get further into the performance thing I can use the tunnel bars at the floor level to attach the harness and switch to a full race seat.
The rear legs were to follow the outline of the rear quarter windows rather than diagonally falling straight to the wheel arches and this resulted in several smaller braces to resist any shearing forces.
The final installation shows the second set of diagonal tubes from the rear wheel arch to the main hoop and the diagonal bar to complete the “not quite half cage but more than a roll bar”. There is discussion of a removable brace between the two main legs at the wheel arch and/or between the two suspension points. May get added later this year.
This could have been done much more efficiently and cheaply if I hadn’t followed the outline of the rear quarter windows and dropped the rear legs straight back to the wheel arches and had two diagonals to the suspension points but the space would have been much less functional for traveling. Getting the bench and carpet backing will be a major pain in the ass and I still have a hole in the roof to fill but I have a much stiffer chassis and some roll over protection.
For next year, Chris gave me some additional suggestions for the front driver/passenger half of the car and I’ve seen some ideas for the engine compartment. I’m enrolled in a welding course through continuing ed at the collage Chris teaches at starting in May but I doubt I’ll ever approach what he can do with metal and a little electricity.
I pick it up tomorrow and start the reassembly.
Doug
I dropped the car off at the home of a welding instructor (Chris McQuay) at a community collage that runs a custom welding and fabrication business –Unobtainium Welding http://www.higherarcing.org/ as a side venture (soon to be full time). My list of requirements included seam welding wherever possible (I did the prep grinding for most of it), main hoop and back legs to follow the line of the windows, one removable diagonal bar in the main hoop, chassis stiffening and repair of some nasty work done when the sunroof was added in the mid 80’s. The ability to leave the rear functional for gear beyond what the trunk could carry on multi day road trips was paramount and had a major influence on design (apparently) and cost (definitely). In addition, I removed all four windows for a thorough cleaning and de-gunking (grease becomes wax after 3 decades) – motors were all fine.
First order of business was gutting of the interior and elimination of the sunroof, which was never something I looked for in any vehicle I’ve owned, though it was fully functional. It’s a hole in the roof, right? It’s Canada, not SO CAL, eh? Motor was in the trunk
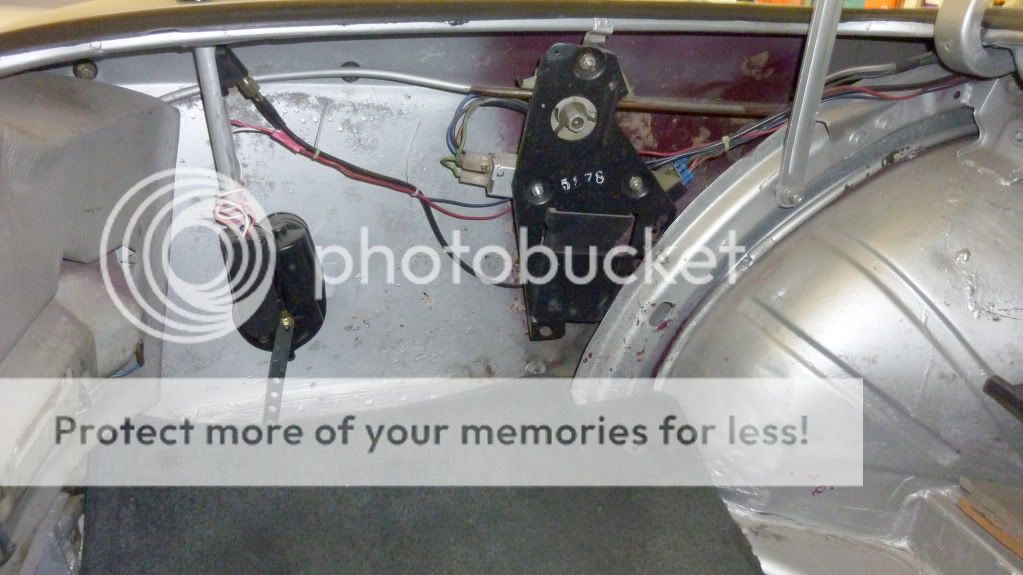
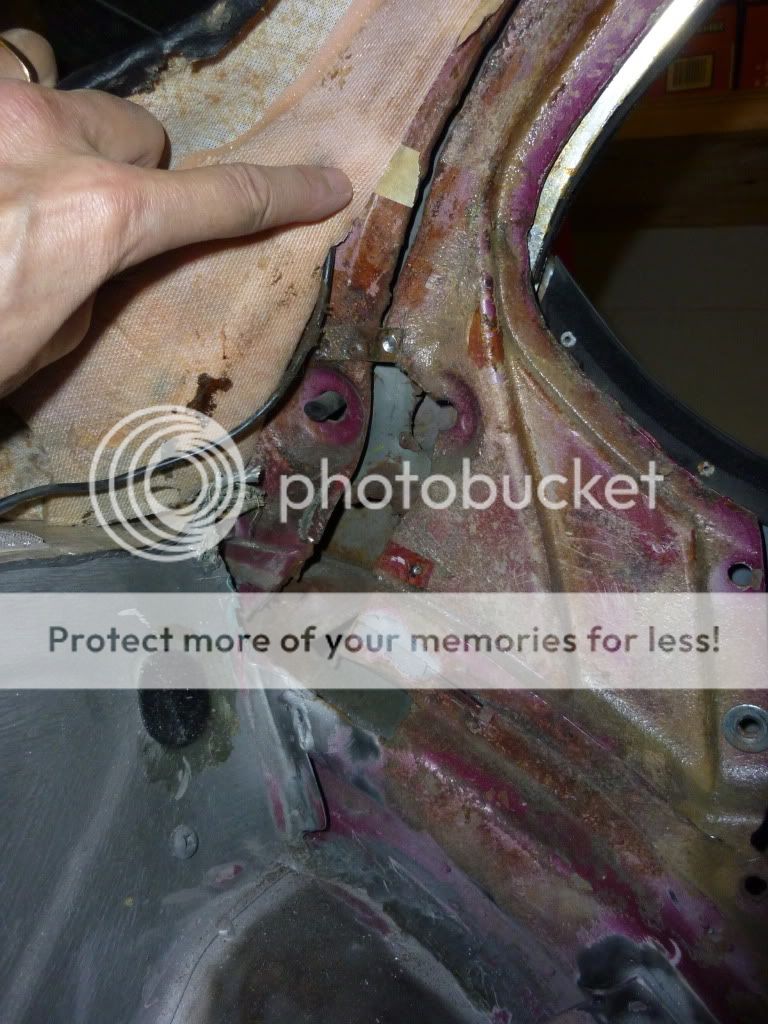
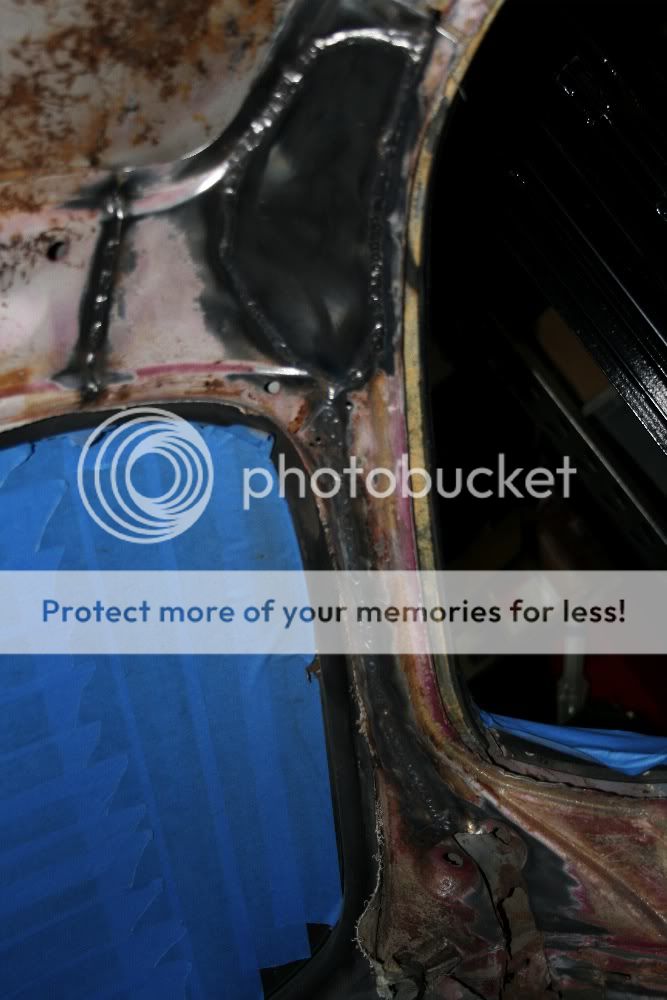
One used sunroof.
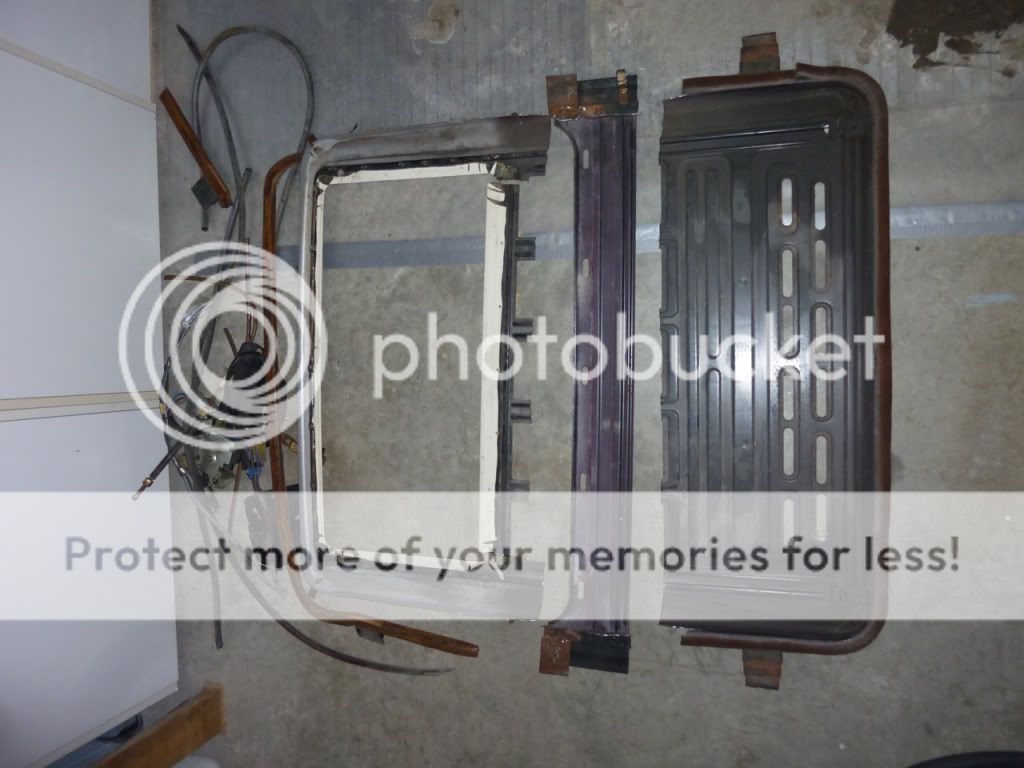
One hole in roof.
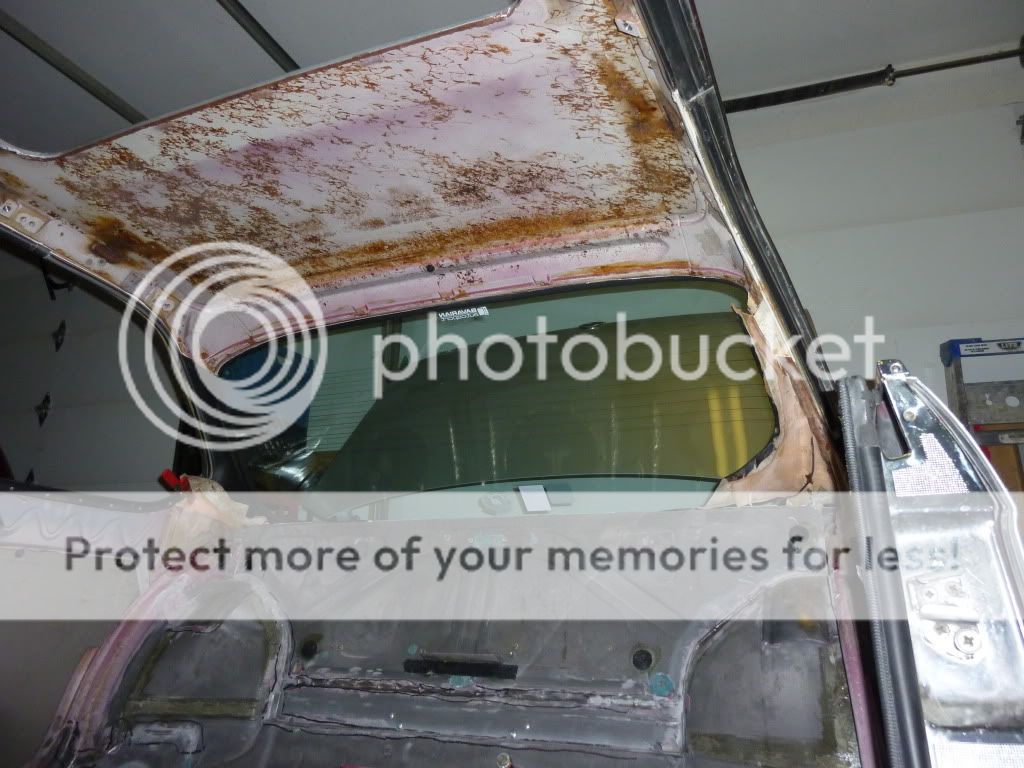
Additional plates were added on the wheel arch, driveshaft hump and the seat bulkhead at the rear quarter window flare.
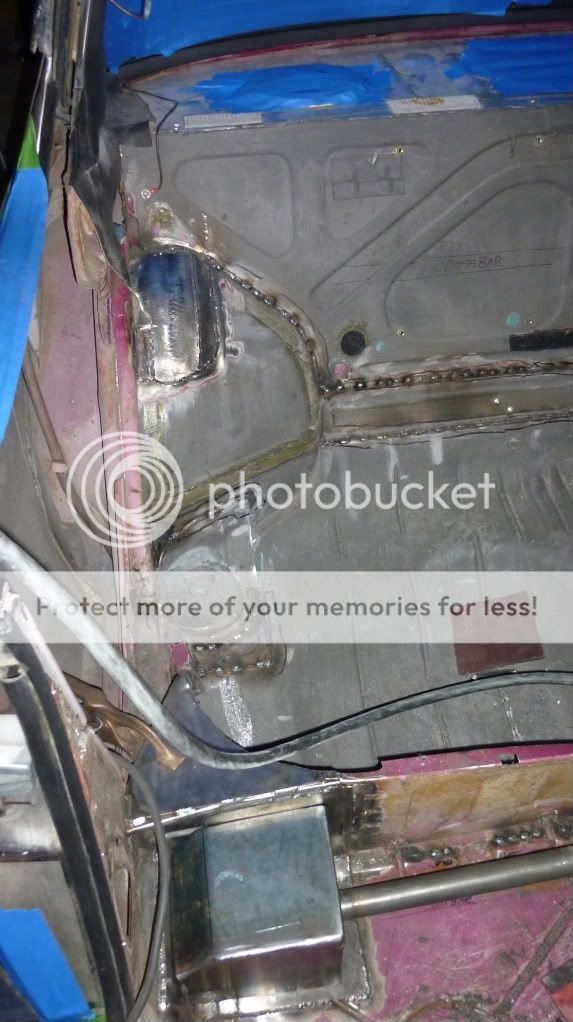
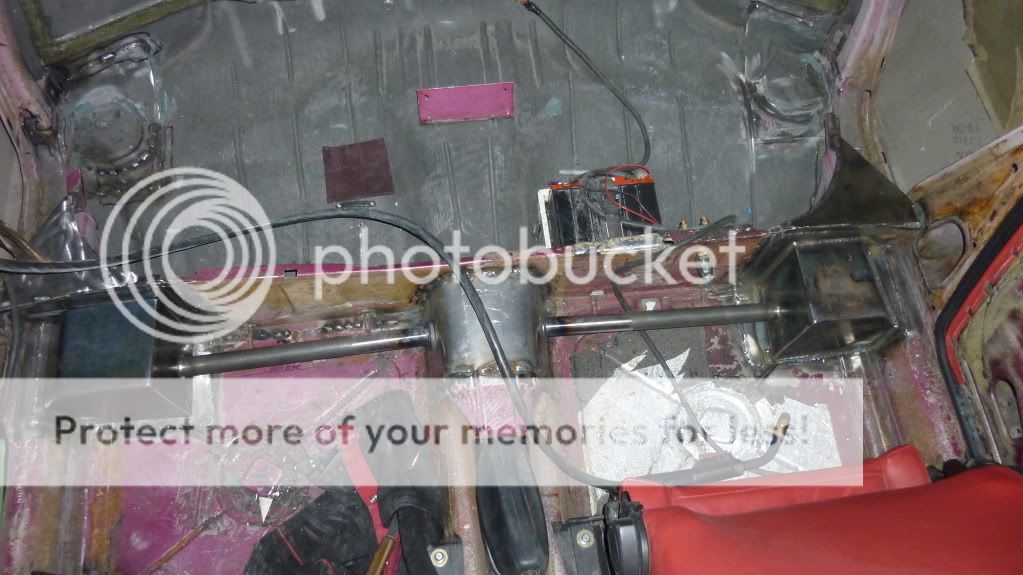
Light gauge plate was fabricated into structural boxes for the main hoop to weld onto that resist punching through the floor and allow access to the 360 joint to be welded. Brace tubes ran from these boxes to the transmission tunnel strengthen the chassis.
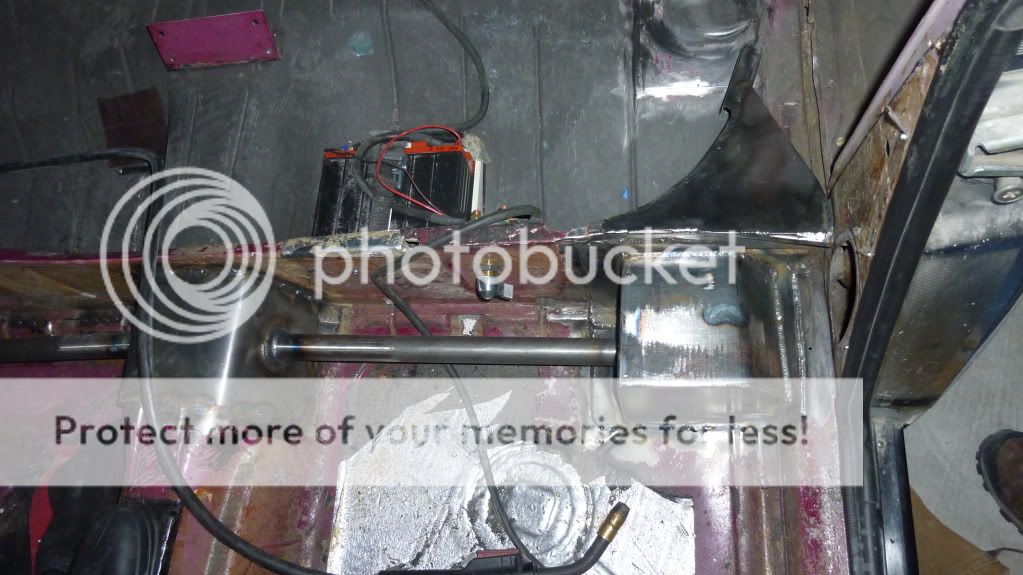
Each of the boxes has a sleeve in which to run all the wiring to rear lights, fuel pump, amps and speakers and batteries.
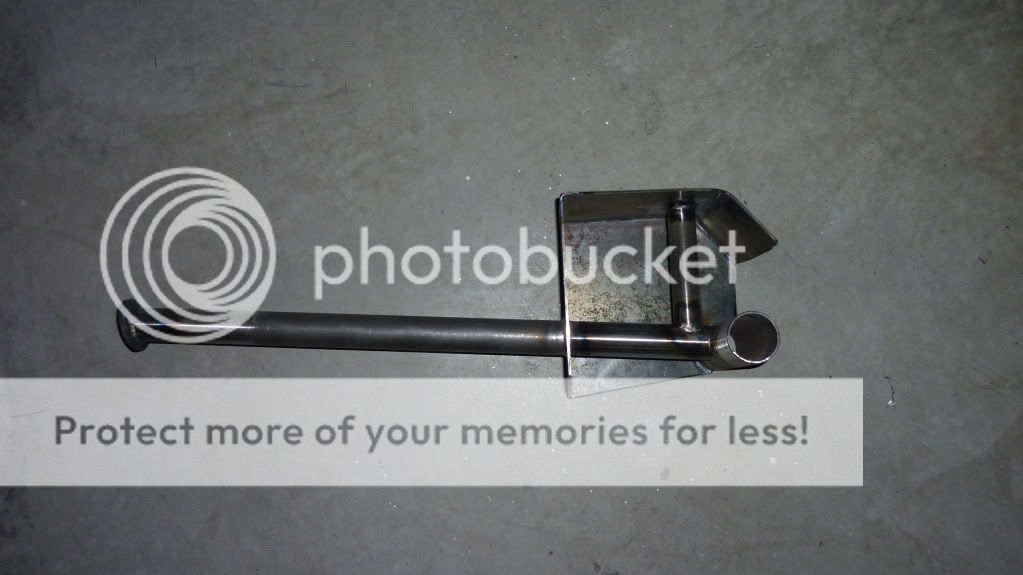
The main hoop has a removable diagonal brace from top driver corner to bottom passenger plus a plate gusset in each of the upper corners. An anchor point was added outboard on both sides of the main hoop for the top swivel bracket for a reproduction 2002 (Coupeking again) 3 point seatbelts.
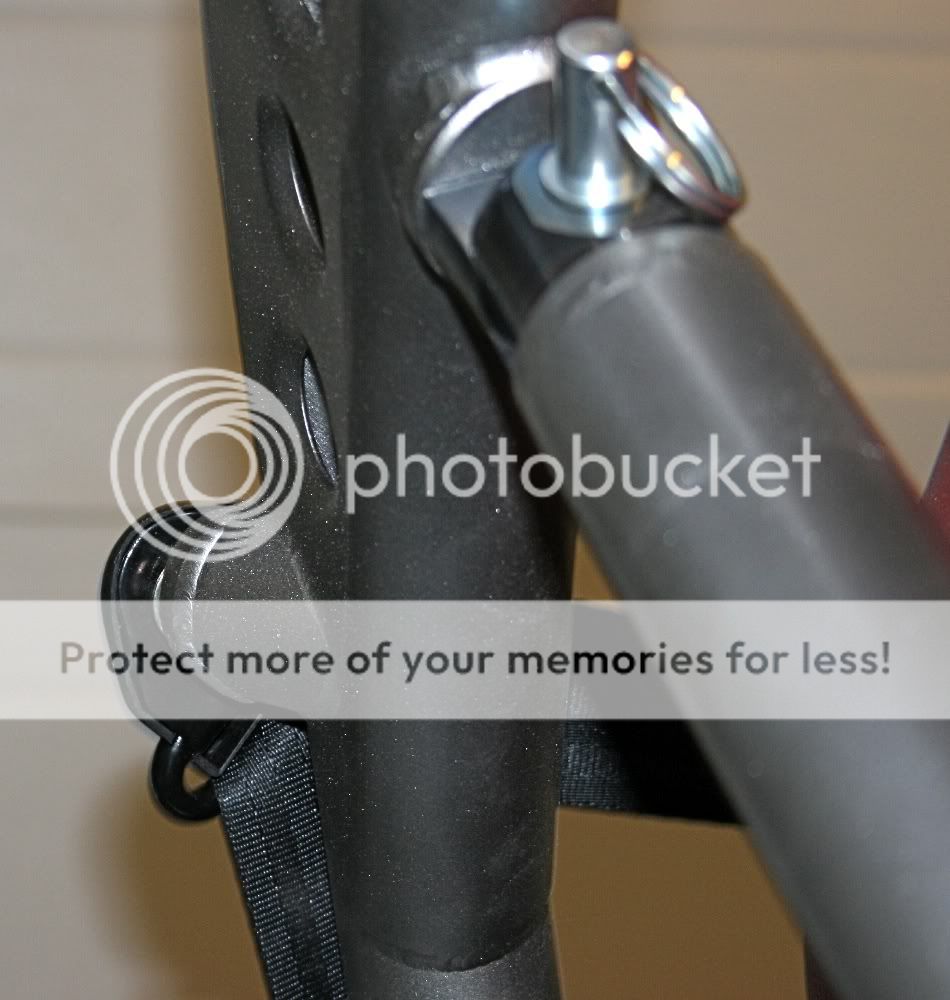
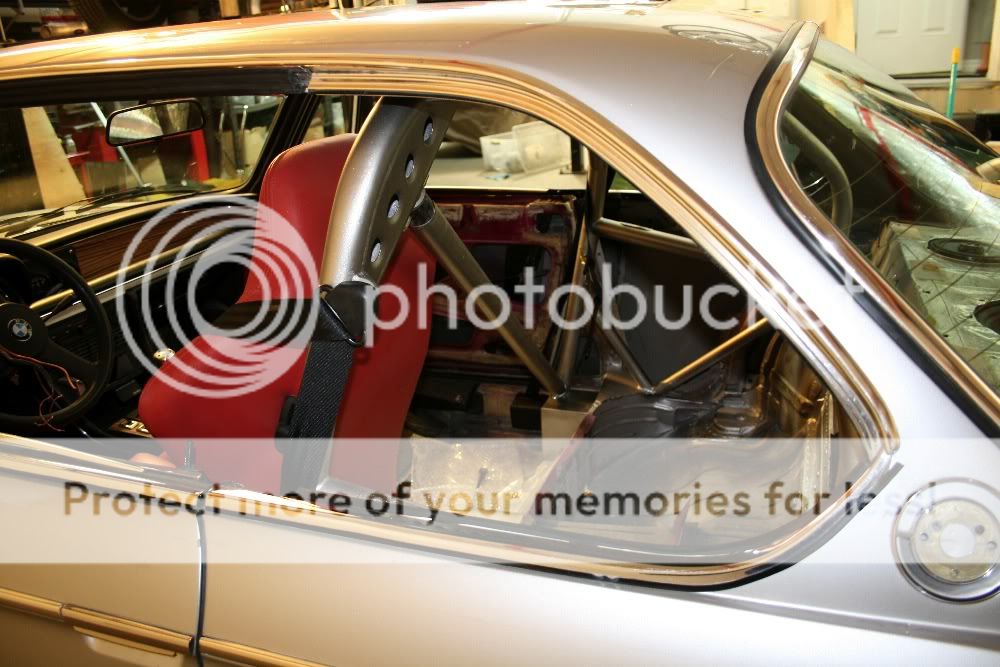
The Recaro SRD seats in the car are not compatible with a four point harness and I’m not willing to give the blissful comfort and support they offer. If I get further into the performance thing I can use the tunnel bars at the floor level to attach the harness and switch to a full race seat.
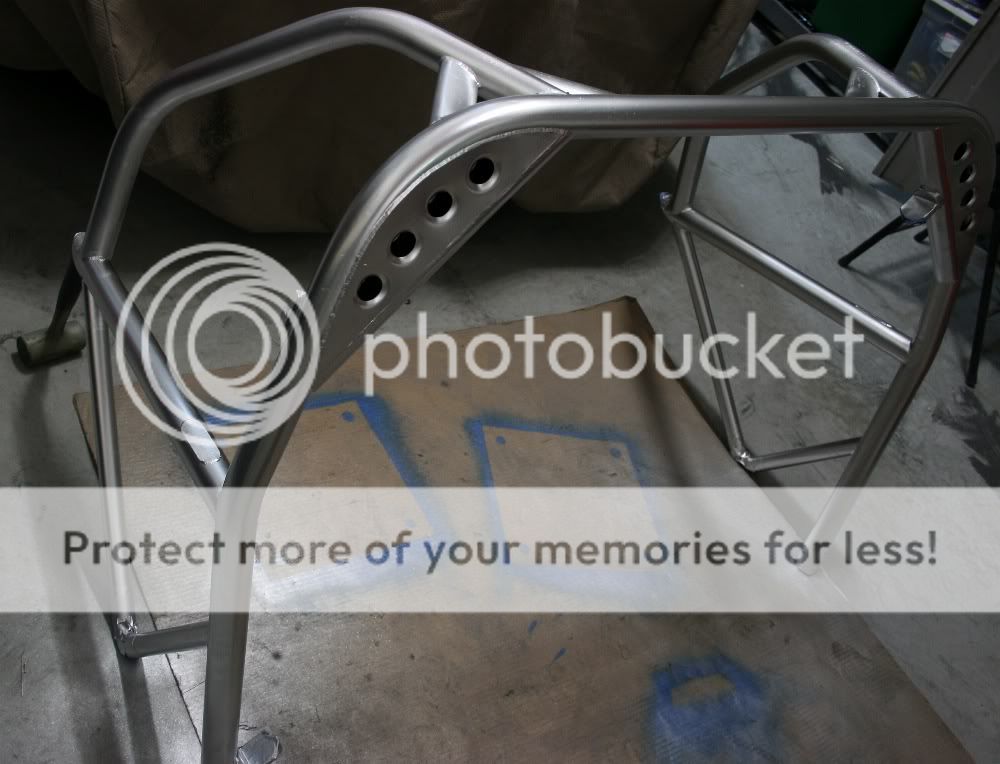
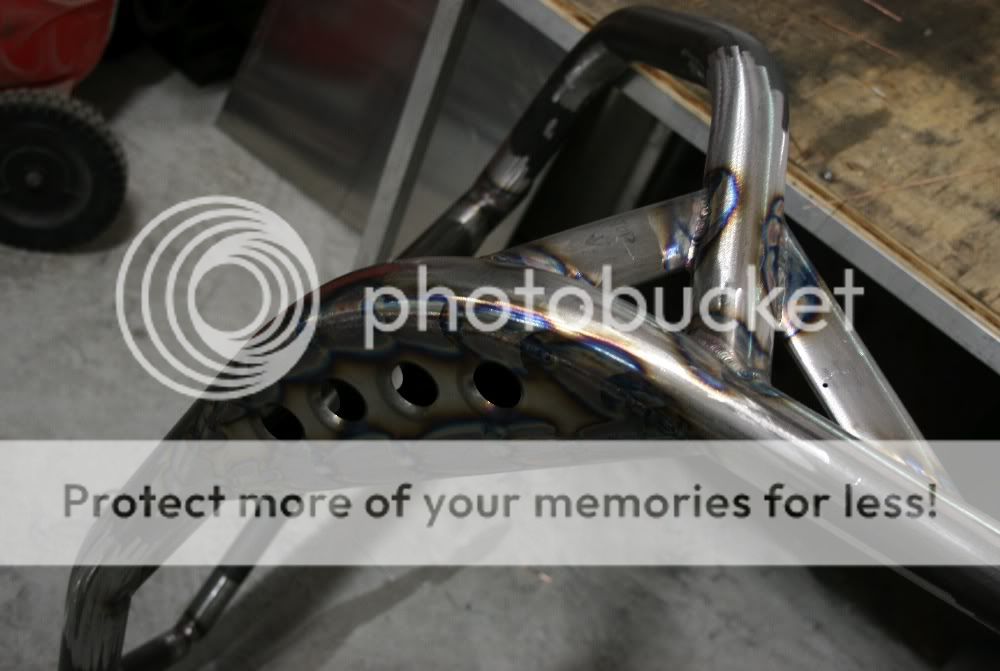
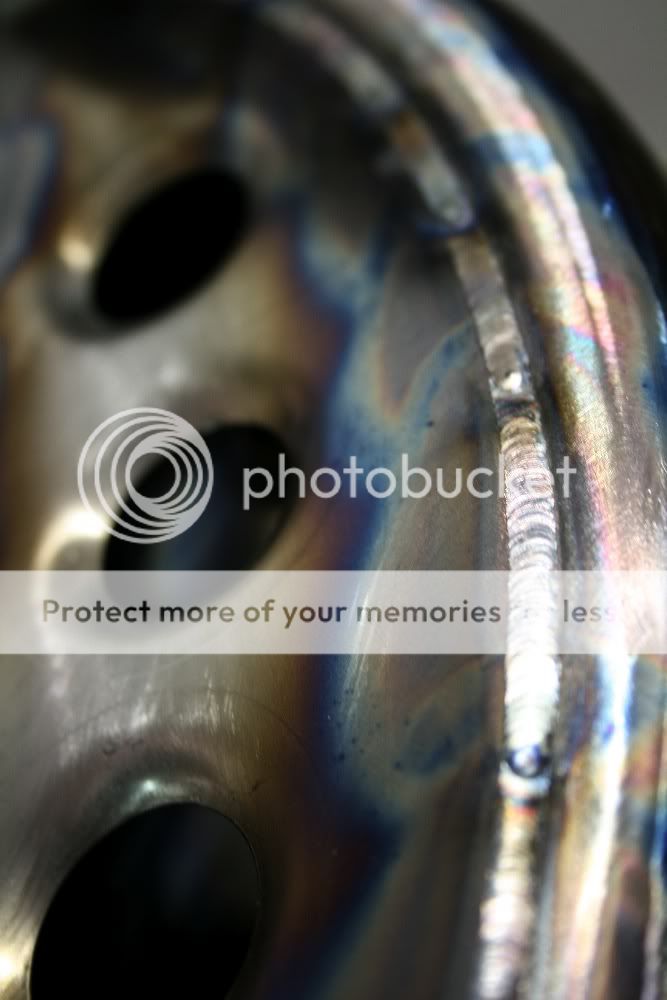
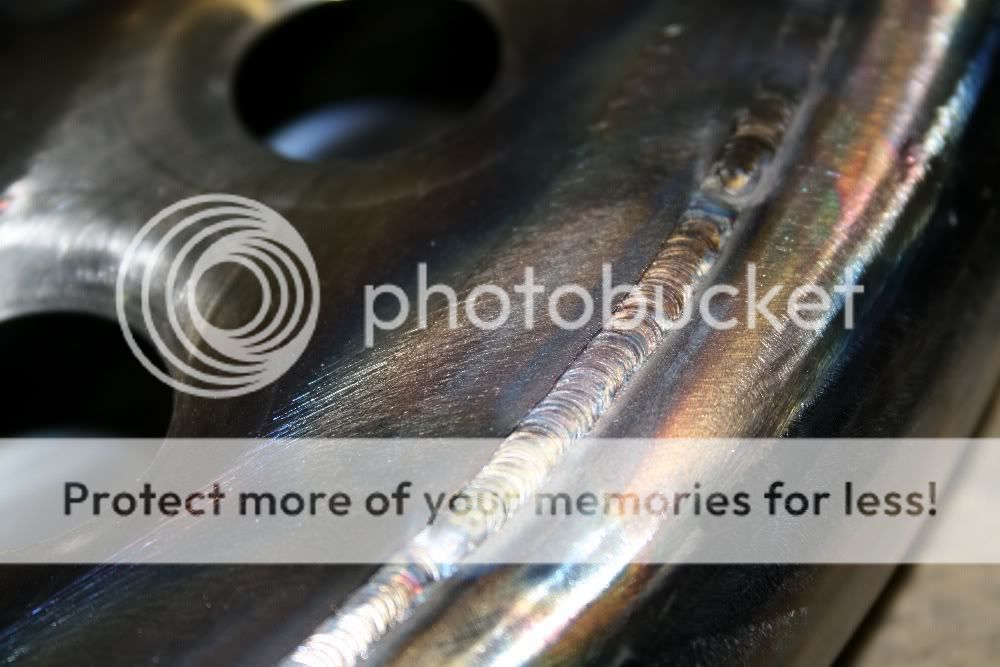
The rear legs were to follow the outline of the rear quarter windows rather than diagonally falling straight to the wheel arches and this resulted in several smaller braces to resist any shearing forces.
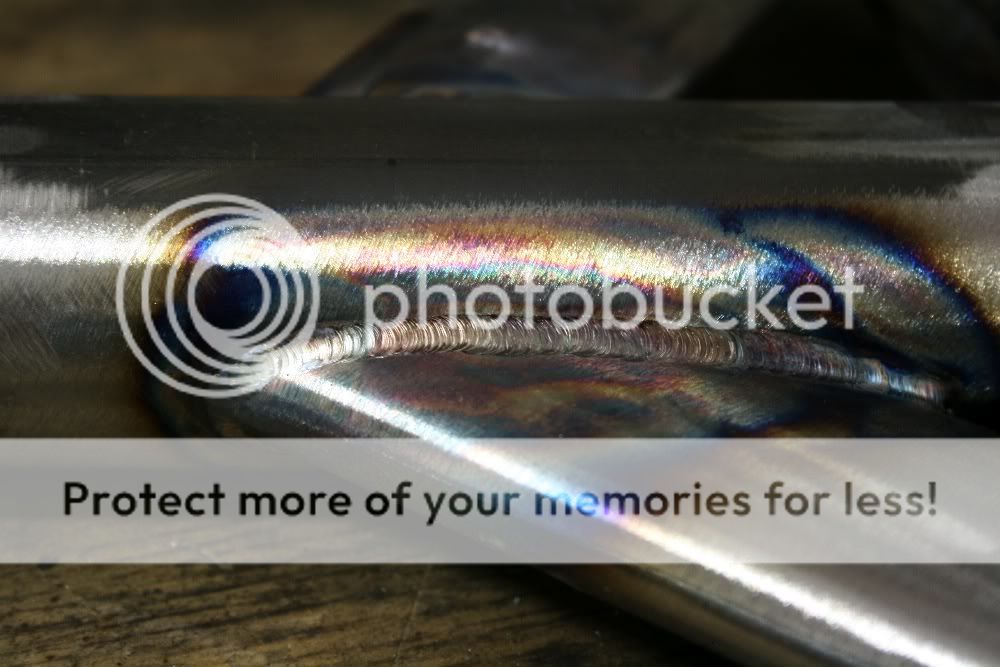

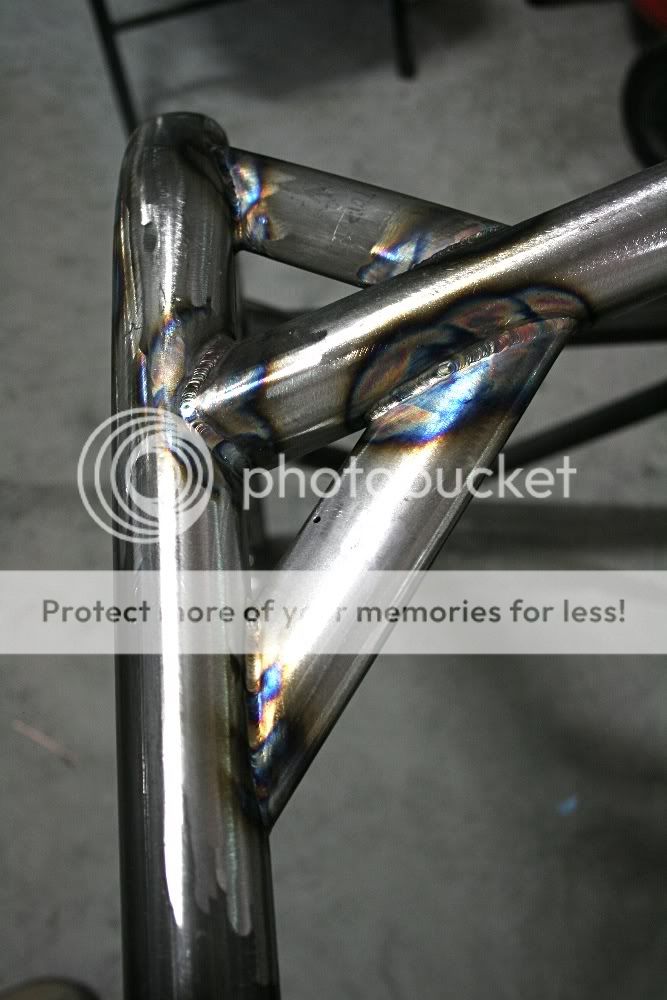
The final installation shows the second set of diagonal tubes from the rear wheel arch to the main hoop and the diagonal bar to complete the “not quite half cage but more than a roll bar”. There is discussion of a removable brace between the two main legs at the wheel arch and/or between the two suspension points. May get added later this year.
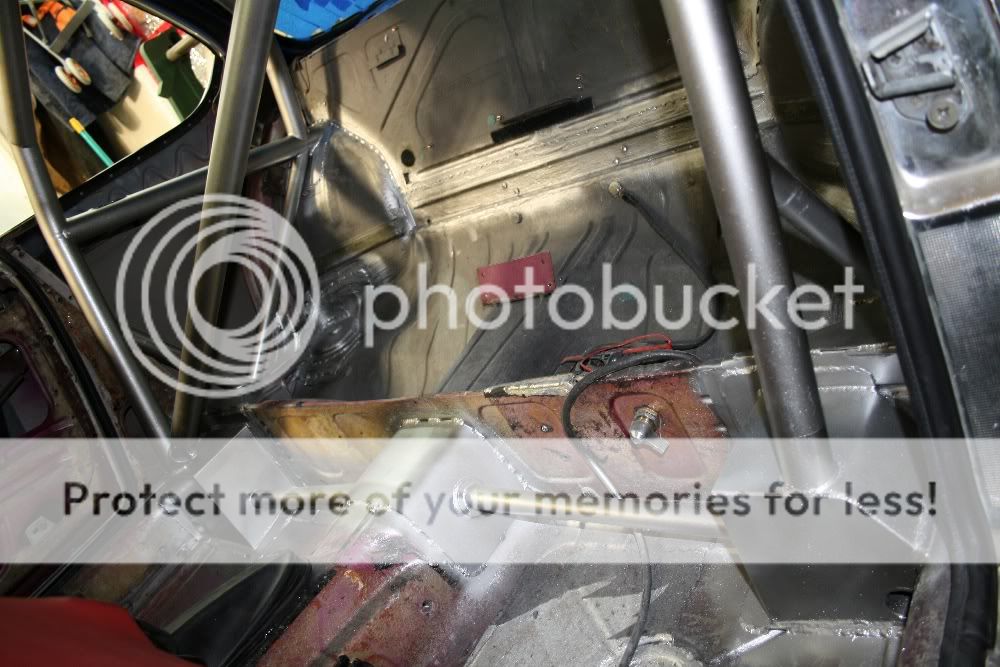
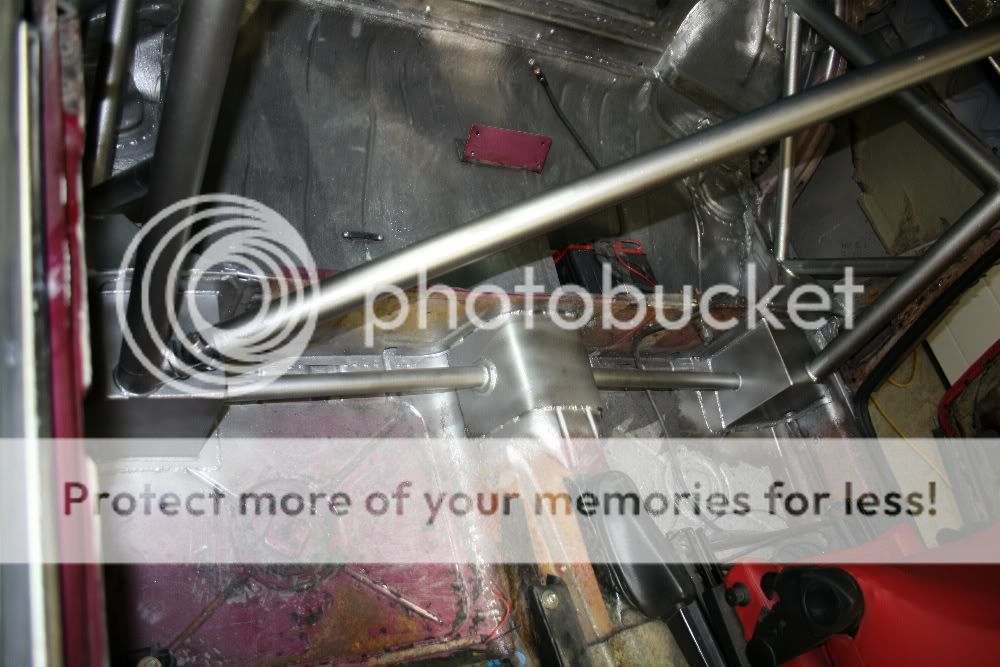
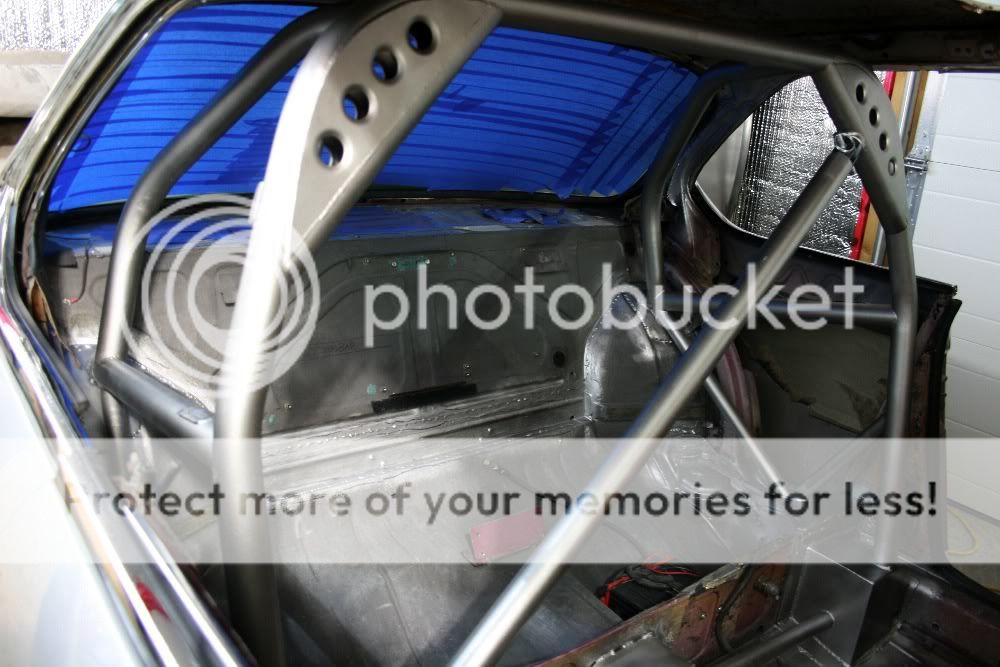
This could have been done much more efficiently and cheaply if I hadn’t followed the outline of the rear quarter windows and dropped the rear legs straight back to the wheel arches and had two diagonals to the suspension points but the space would have been much less functional for traveling. Getting the bench and carpet backing will be a major pain in the ass and I still have a hole in the roof to fill but I have a much stiffer chassis and some roll over protection.
For next year, Chris gave me some additional suggestions for the front driver/passenger half of the car and I’ve seen some ideas for the engine compartment. I’m enrolled in a welding course through continuing ed at the collage Chris teaches at starting in May but I doubt I’ll ever approach what he can do with metal and a little electricity.
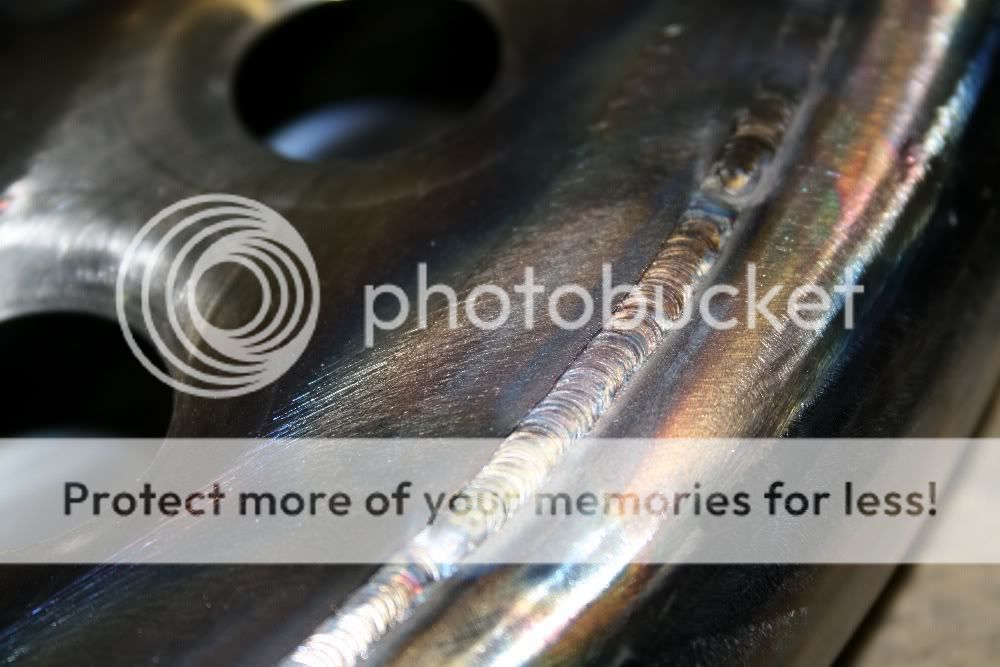
I pick it up tomorrow and start the reassembly.
Doug
Last edited: