- Messages
- 292
- Reaction score
- 74
Hello friends, here I will chronicle my portion of the restoration and modification of this E9. I've been employed by the owner to finish the work on this car, it's not mine sadly, although it's giving me an itch to find one. Hopefully some of my ideas and experiences will be of use to someone. I'm working on it about 40 hours a week so hopefully this thread will be fast paced and interesting.
The car came to me already painted (space grey metallic, a newer BMW color), and with a rebuilt M30B34 engine that would turn out to have some problems. Suspension was rebuilt, but no brakes are installed. Everything else is pretty much in boxes.
I started off by removing the engine, as it had no fuel injection system or the transmission attached to it. While waiting for some engine parts I set about connecting the new small brake booster to the pedal. I found the booster bracket had been shortened to the point the clutch master cylinder could not fit and did not align properly with the pedal. So I made a new front end for the bracket and welded a portion of the old booster extension rod to the new booster to reach the pedal. I ended up doing a lot of re-bending on the brake pipes to make them nice and neat.
As it was:
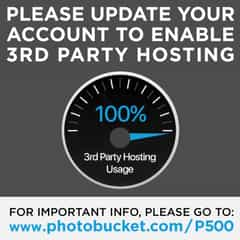
Had to put the enigne back in for a minute to make sure my proposed booster location wouldn't hit anything...
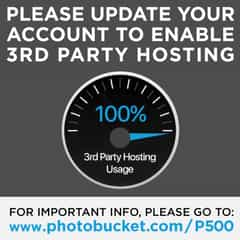
Remodified:
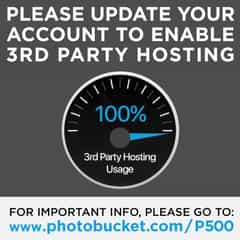
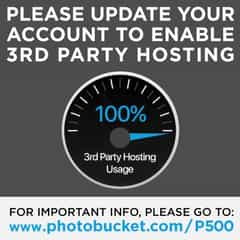
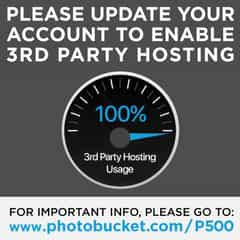
And all done:
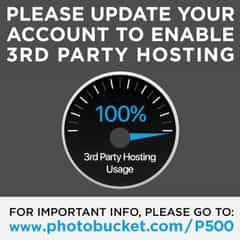
At the same time, I found a fuel pump that would be suitable for the conversion to EFI. This is a kit from Tanks Inc. The only thing I could find that included a trough at the bottom to prevent fuel starvation. With any other option I would have had to add one somehow, probably by cutting a hole in the bottom of the tank and welding a trough in. This seemed like a good option and fits the shape of the tank well.
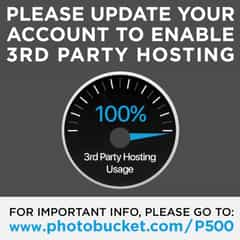
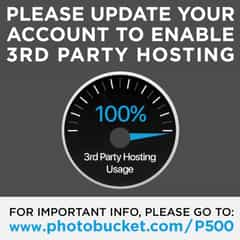
Most of the clutch mechanism was missing so I had to buy new parts for that. All of the old-style clutch stuff is crazy expensive but all still available which is good.
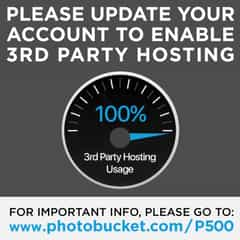
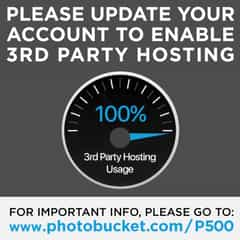
The car came to me already painted (space grey metallic, a newer BMW color), and with a rebuilt M30B34 engine that would turn out to have some problems. Suspension was rebuilt, but no brakes are installed. Everything else is pretty much in boxes.
I started off by removing the engine, as it had no fuel injection system or the transmission attached to it. While waiting for some engine parts I set about connecting the new small brake booster to the pedal. I found the booster bracket had been shortened to the point the clutch master cylinder could not fit and did not align properly with the pedal. So I made a new front end for the bracket and welded a portion of the old booster extension rod to the new booster to reach the pedal. I ended up doing a lot of re-bending on the brake pipes to make them nice and neat.
As it was:
Had to put the enigne back in for a minute to make sure my proposed booster location wouldn't hit anything...
Remodified:
And all done:
At the same time, I found a fuel pump that would be suitable for the conversion to EFI. This is a kit from Tanks Inc. The only thing I could find that included a trough at the bottom to prevent fuel starvation. With any other option I would have had to add one somehow, probably by cutting a hole in the bottom of the tank and welding a trough in. This seemed like a good option and fits the shape of the tank well.
Most of the clutch mechanism was missing so I had to buy new parts for that. All of the old-style clutch stuff is crazy expensive but all still available which is good.
Last edited: