Marc-M
Well-Known Member
I always knew that the door bottoms were shot at, so I ordered up the door bottom repair section from Walloth& Nesch.
I have to say they are a fantastic reproduction and needed no modification to get a good fit.
So, chopped the bottom out and welded it in – simples!
Next is to repair the Ally door skin - then ensure it fits .
I have to say they are a fantastic reproduction and needed no modification to get a good fit.
So, chopped the bottom out and welded it in – simples!
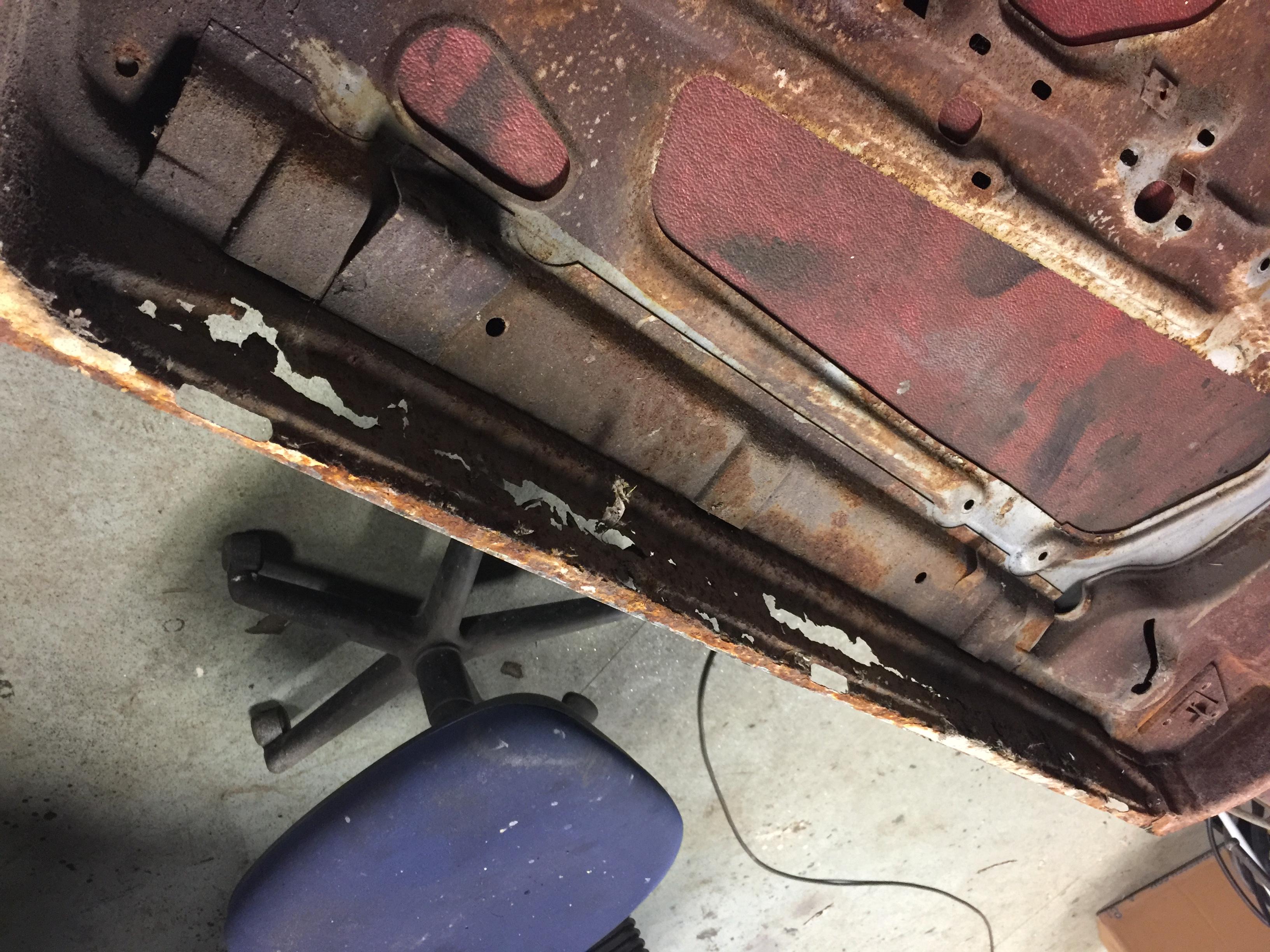
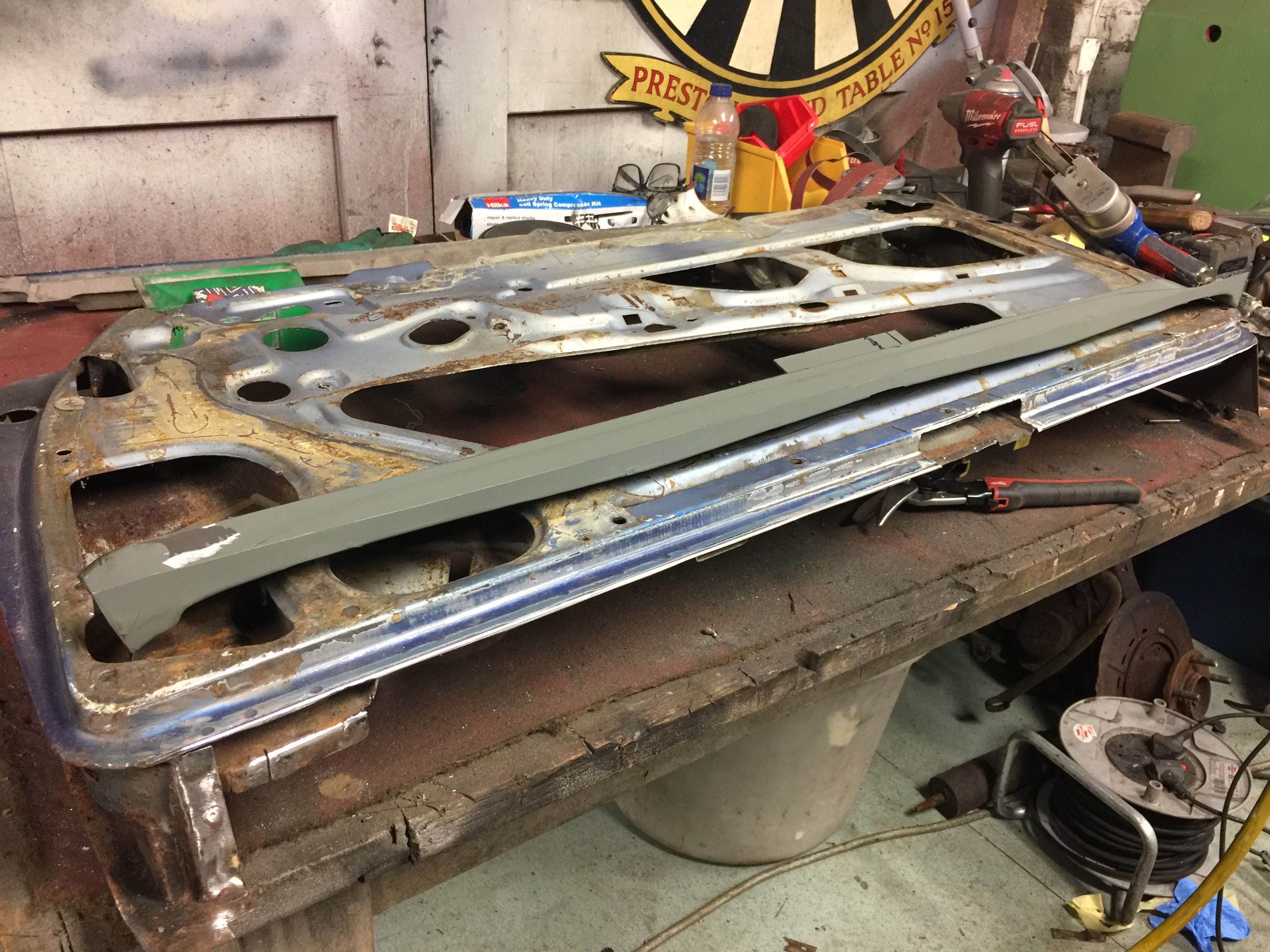
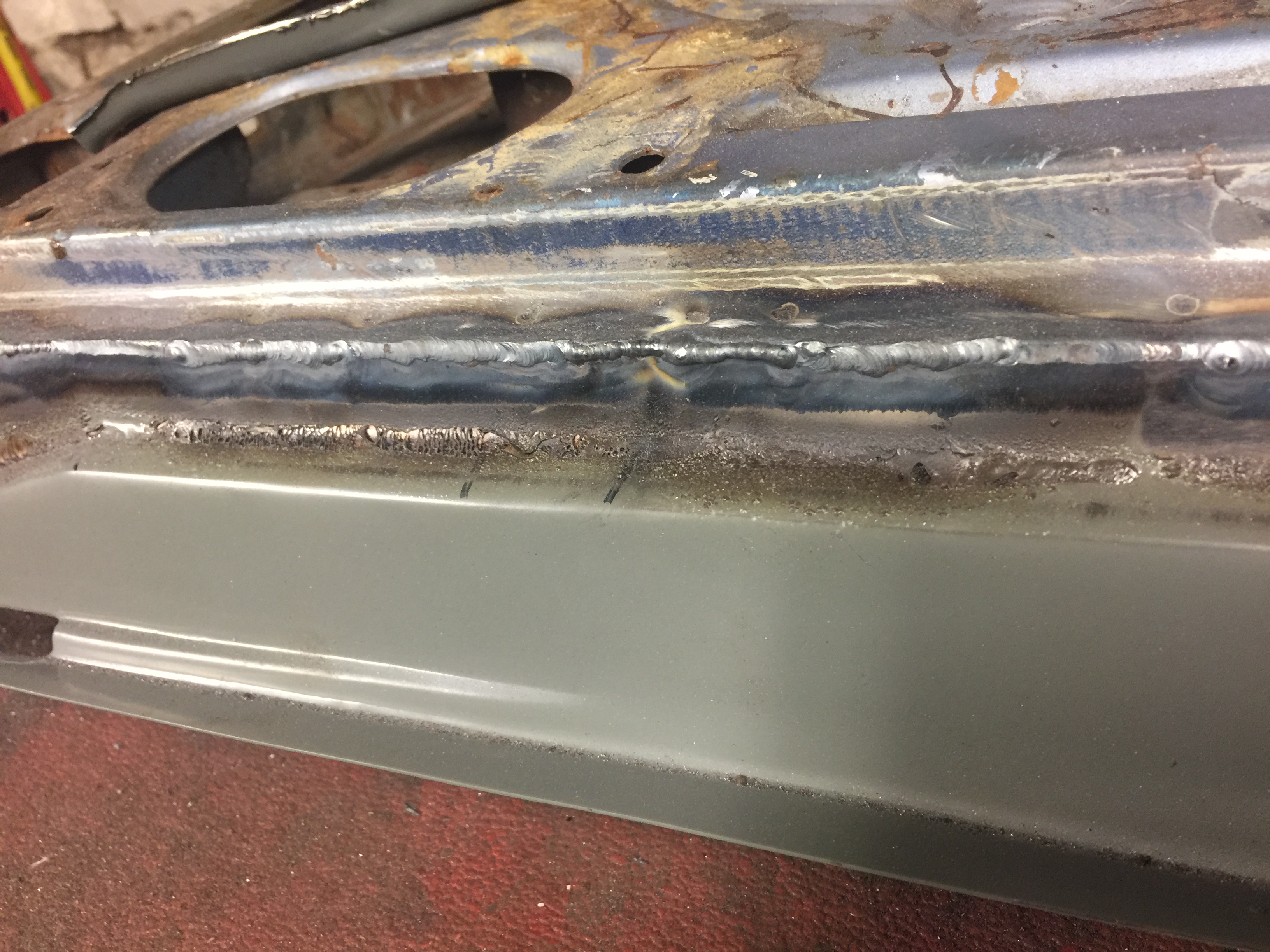
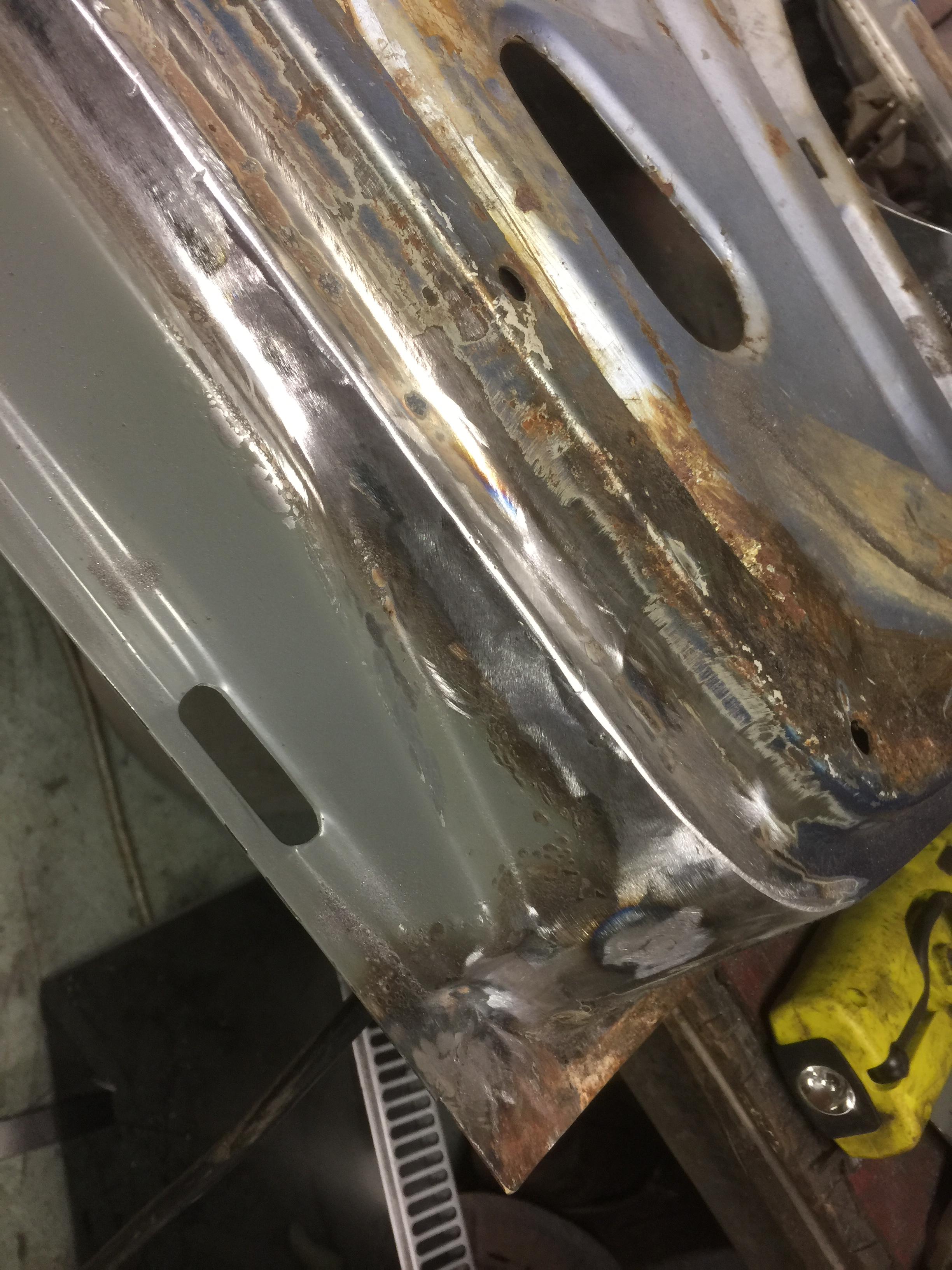
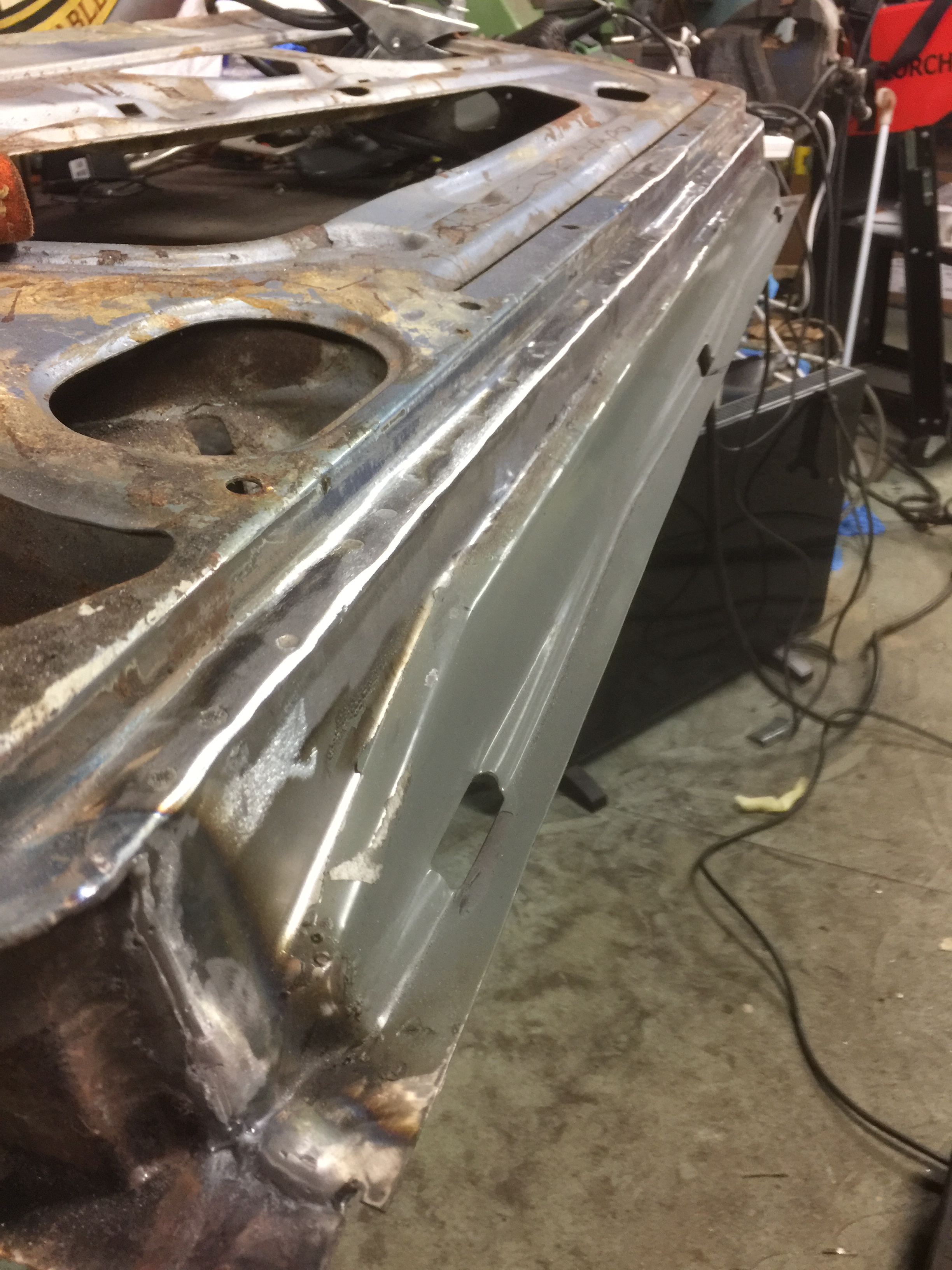
Next is to repair the Ally door skin - then ensure it fits .