Marc-M
Well-Known Member
The water channel that is hidden inside the top of the rear wing was totally rotted out on the LHS, as you can see from the pictures a new section had to be made.
The curvature of the channel was going to be a problem to make as it was quite extreme so I made up a wooden buck and used that to form both halves of the channels.
These took a while as the was a large amount of shrinking required.
The 2 halves were mated up and tig welded together – all I need to do now is braze in the waste tube.
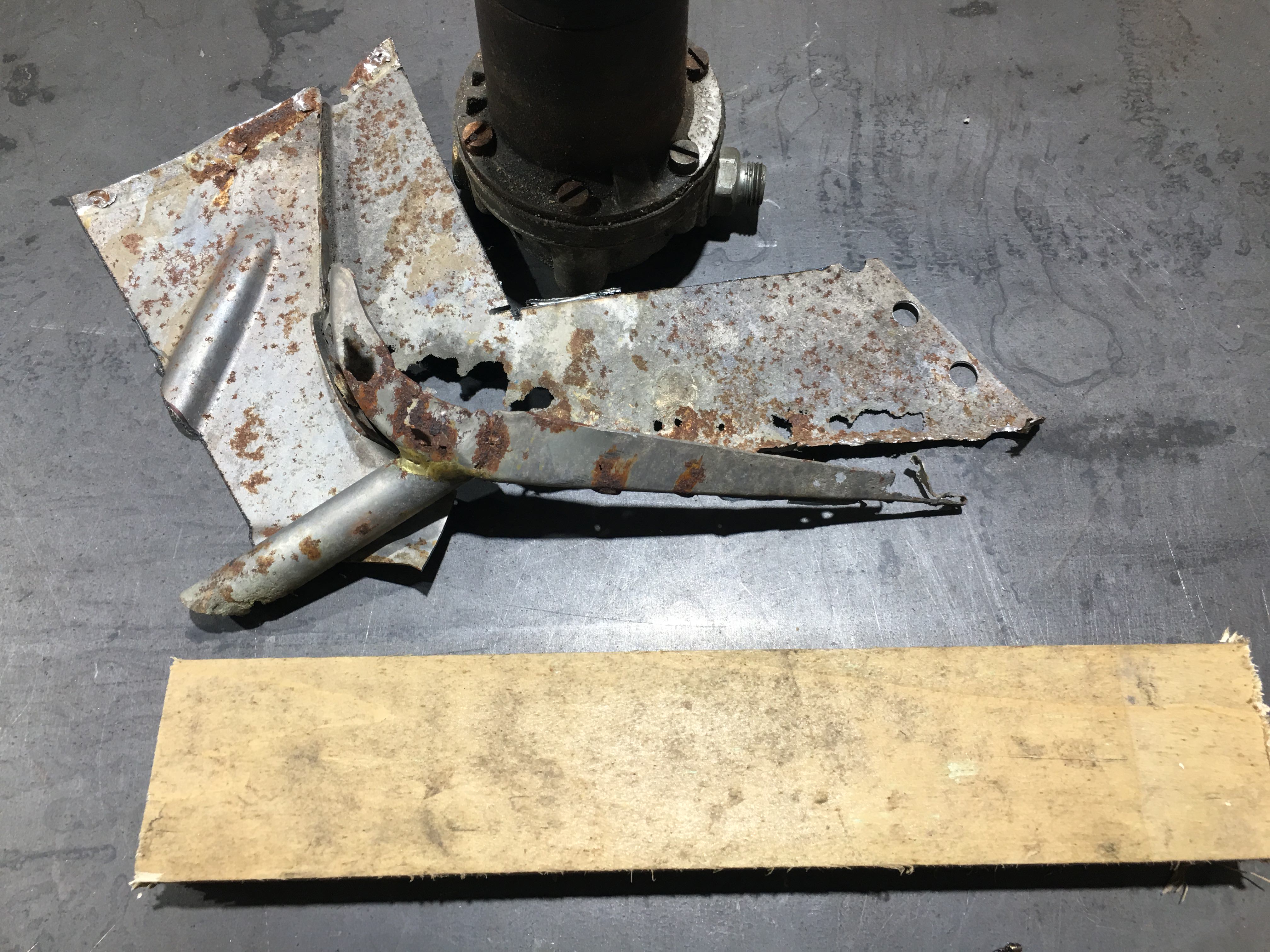
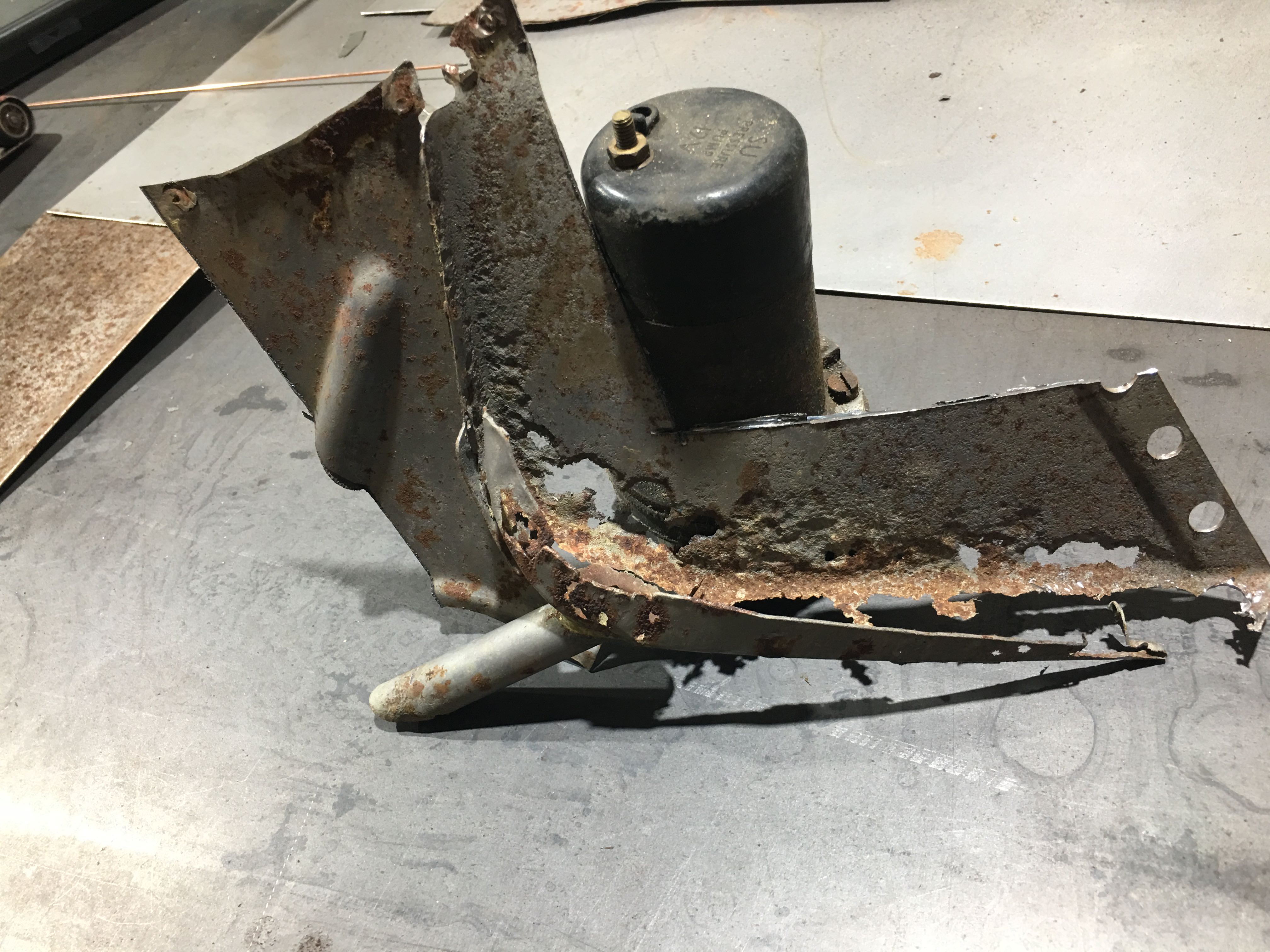
The curvature of the channel was going to be a problem to make as it was quite extreme so I made up a wooden buck and used that to form both halves of the channels.
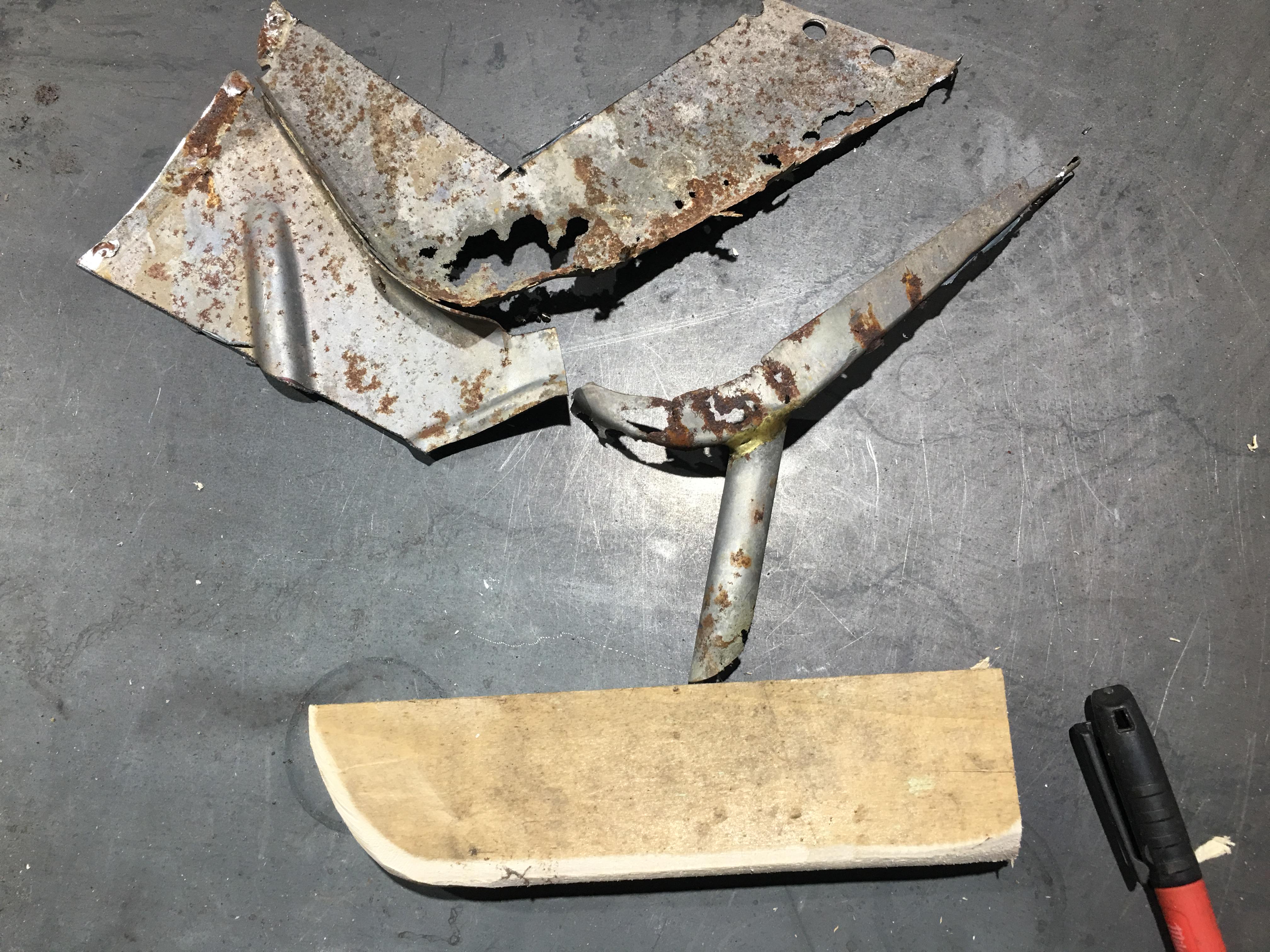
These took a while as the was a large amount of shrinking required.
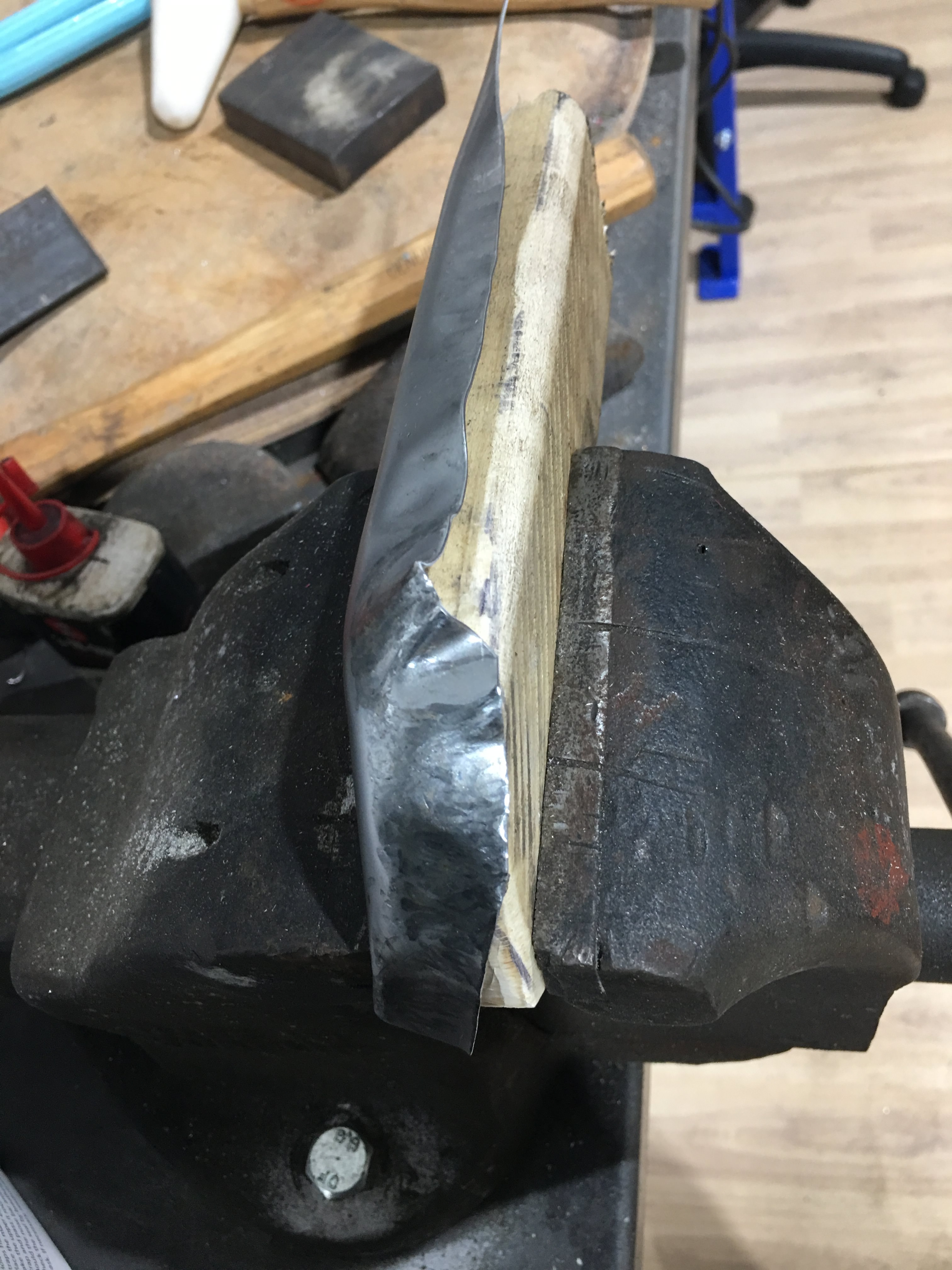
The 2 halves were mated up and tig welded together – all I need to do now is braze in the waste tube.
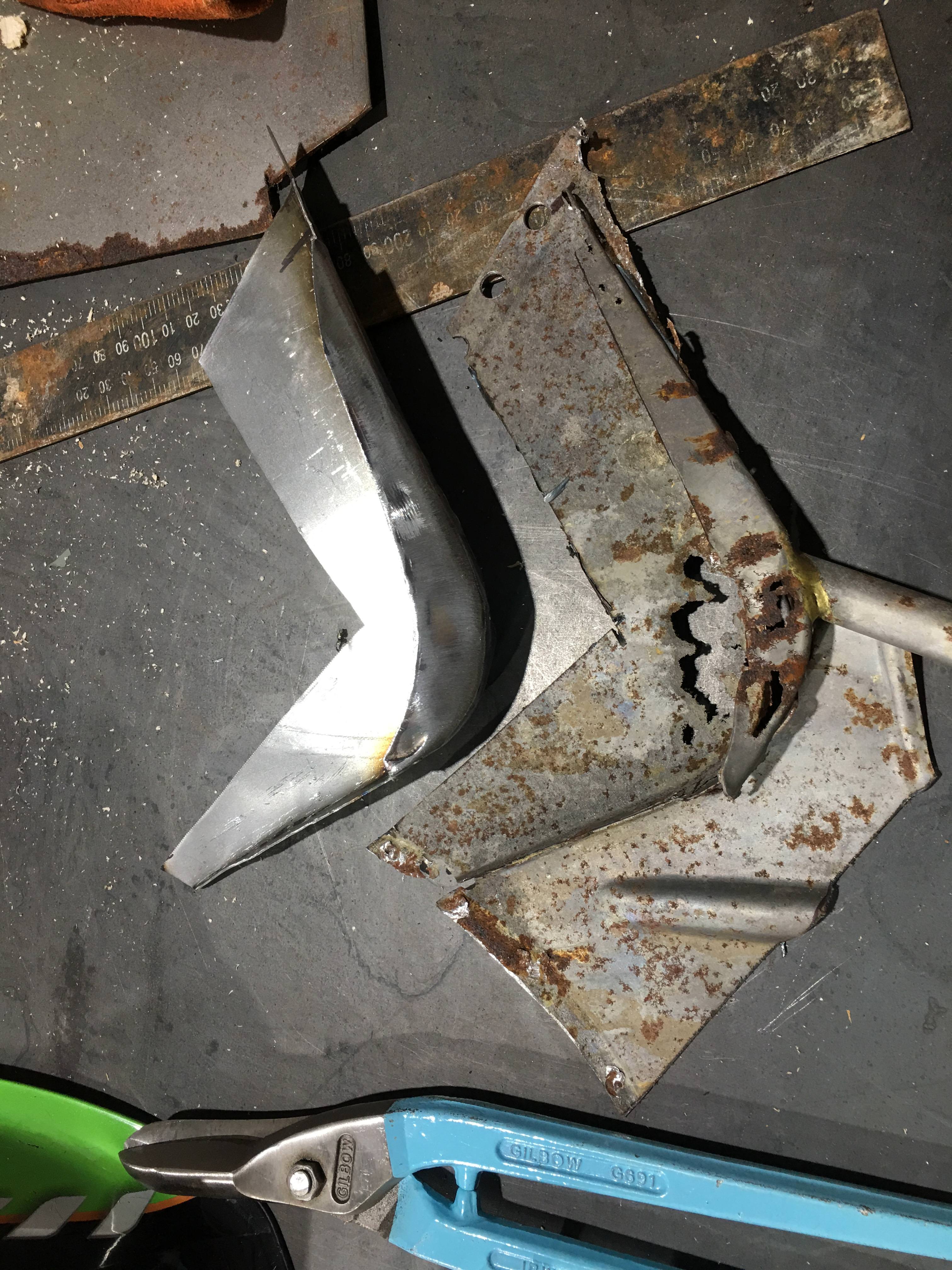