Marc-M
Well-Known Member
Building up the nose cone is turning into quite an epic task.
I have made and welded in the 1st section for bottom together with the radiator mounts, and now as it’s a stable section I have screwed all the panels together to trail fit.
Just as well, it all screwed together quite well, and with a mixture of original BMW parts and repro parts there was no need of a tapping stick to re align the panels.
With it all screwed together I can now make a template of the last section that strengthens the bottom panel that welds to the new section I have made. I have no clue as to what this panel is called, maybe its called –the radiator scuttle lower reinforcement support section?????
I think I’m only a few nights from completing the nose now!
I have made and welded in the 1st section for bottom together with the radiator mounts, and now as it’s a stable section I have screwed all the panels together to trail fit.
Just as well, it all screwed together quite well, and with a mixture of original BMW parts and repro parts there was no need of a tapping stick to re align the panels.
With it all screwed together I can now make a template of the last section that strengthens the bottom panel that welds to the new section I have made. I have no clue as to what this panel is called, maybe its called –the radiator scuttle lower reinforcement support section?????
I think I’m only a few nights from completing the nose now!
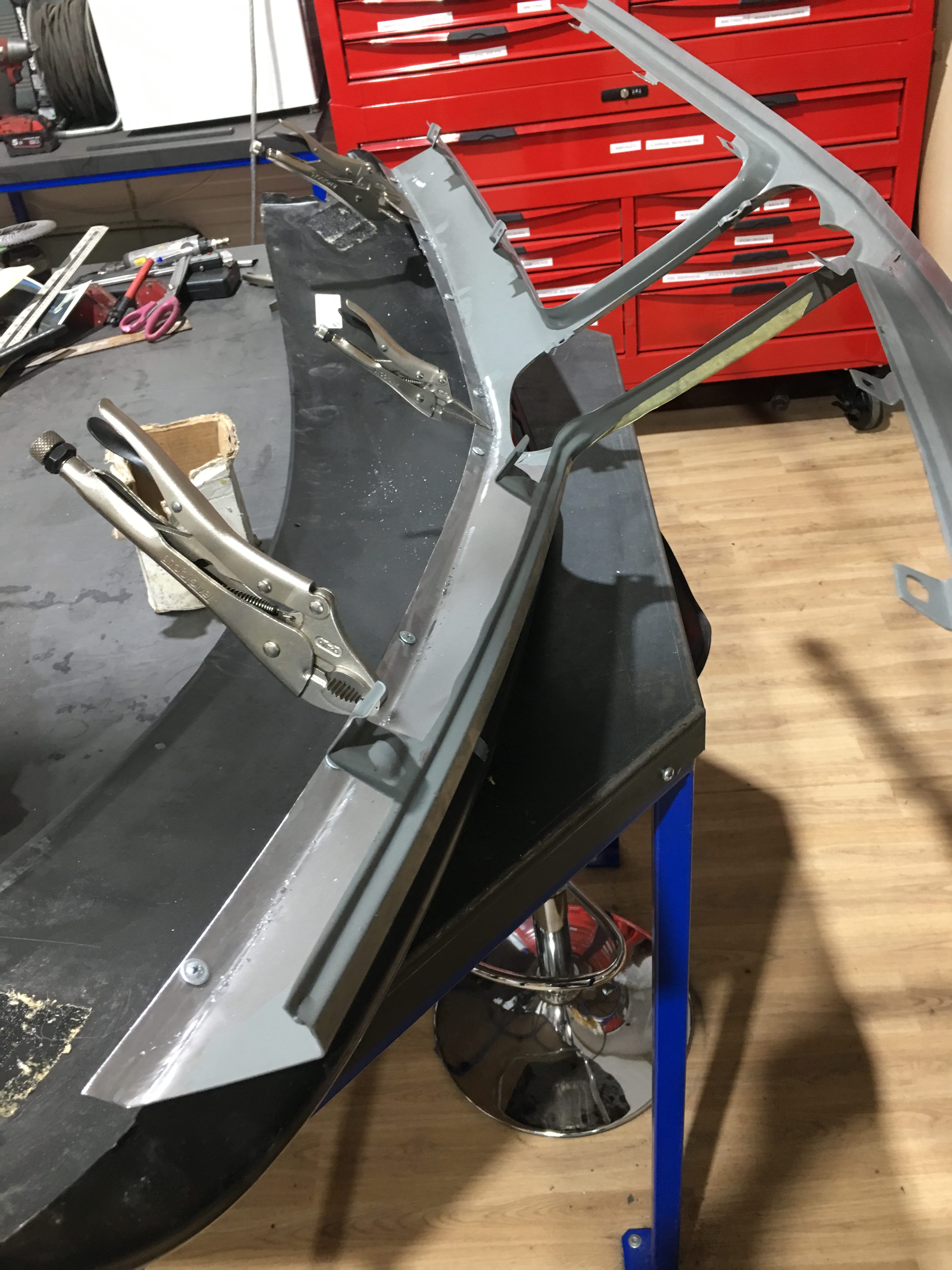
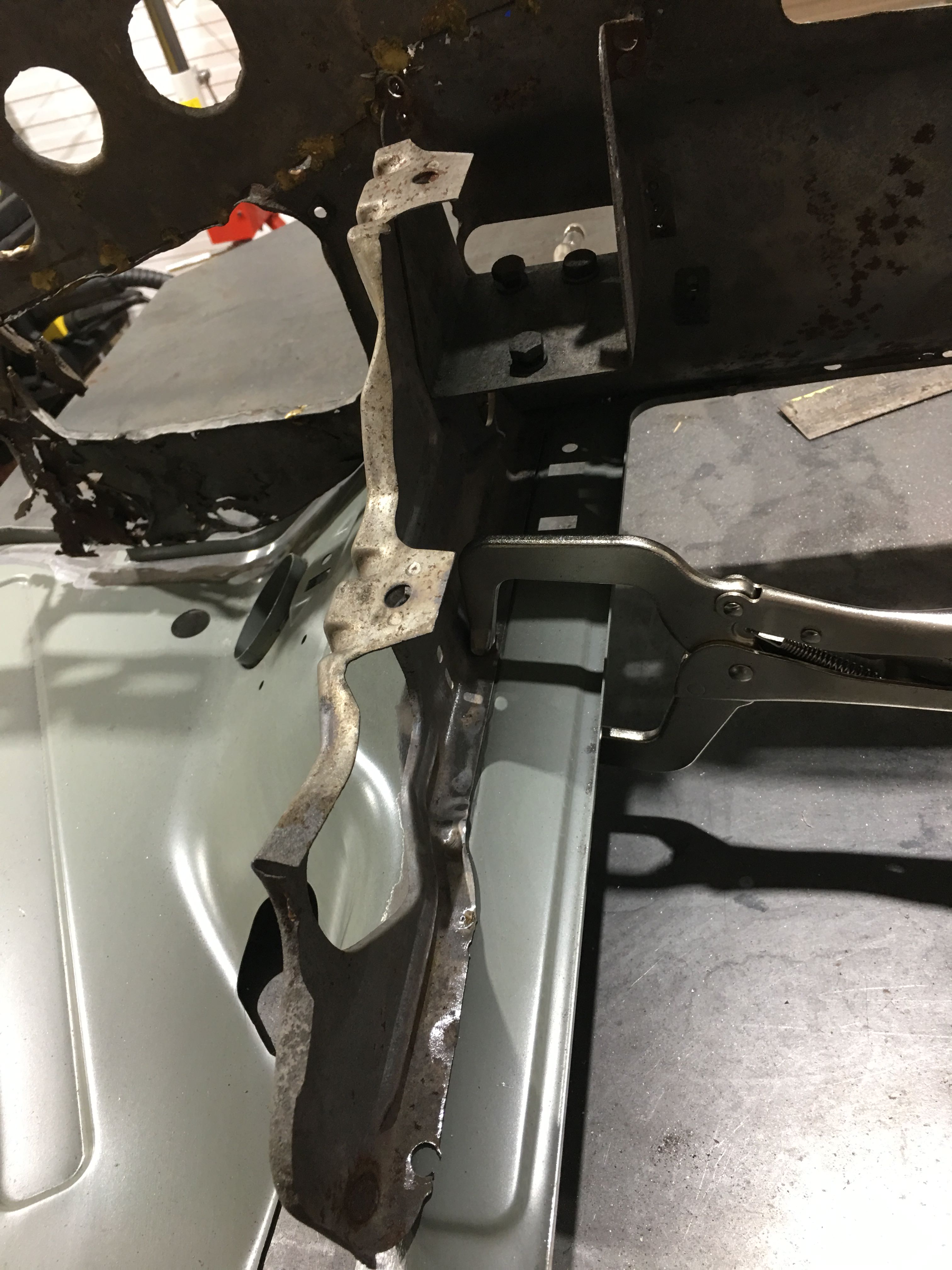
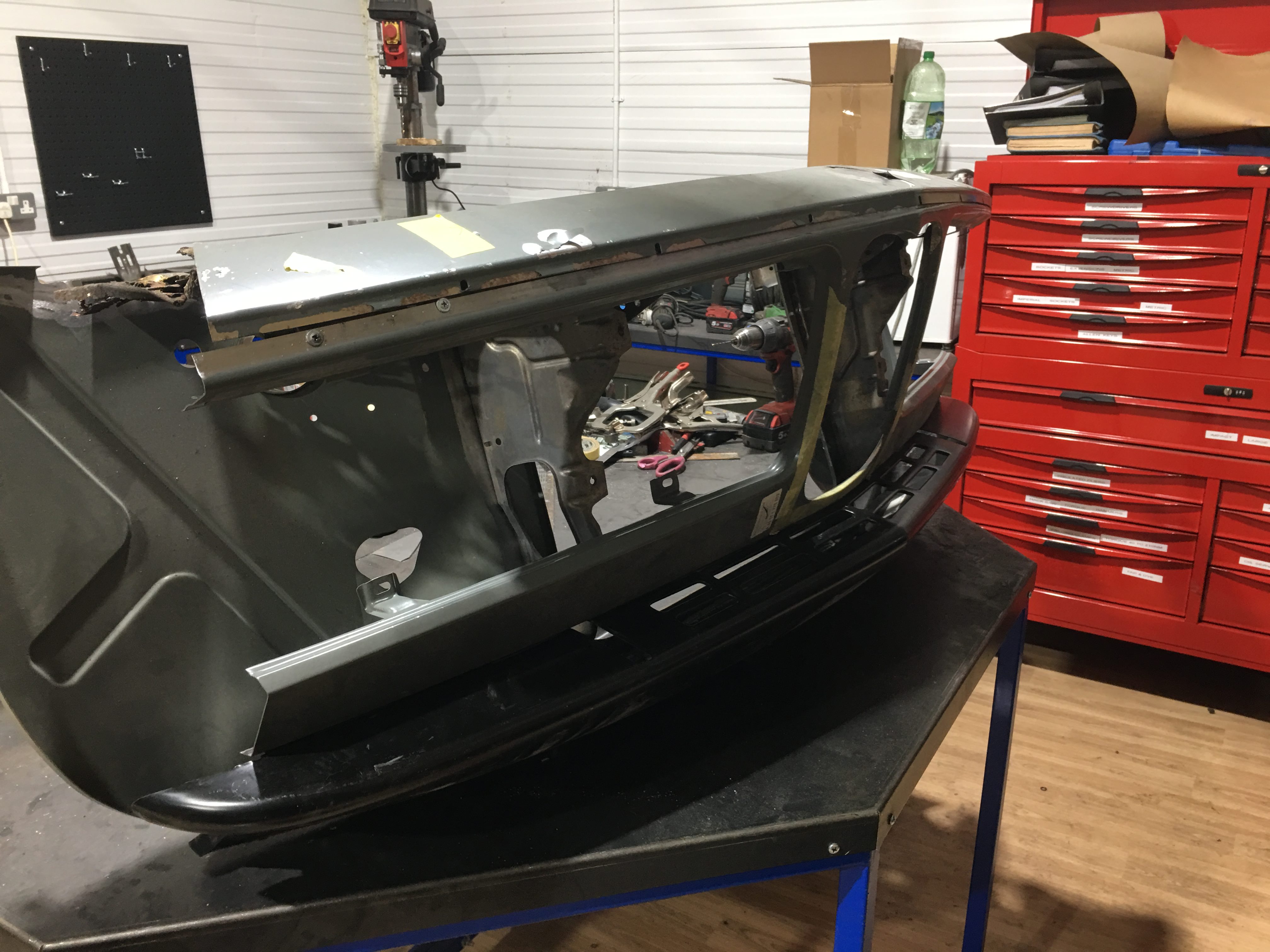