As I have finished the rear quarter panels, I am now focussing on the front end of my car. I have rust holes through the top sheet around the right strut. The Left side will likely have rust underneath as well.
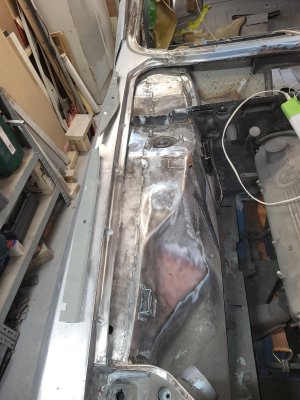
What i can can also clearly see is that my complete front end has been chopped of at one point in its life:
- the front chin panel is post mid-1973 as it has the shorter air vent slots to accommodate for the larger US bumpers.
- there are numerous MIG welds on the front fenders to the connecting parts
- the 4 individual connecting parts, 2 left, 2 right, are missing between the outside fender and the inner fender (in the picture those 2 W&N replacement parts are on the fender).
Now my question is the following: I think that the resulting position of the front of the car is about 7 mm (1/3rd of an inch) lower vs what it should be. I see 2 things that give me that idea:
- the top edge of the strut support panel lies about 7 mm higher then the inner edge of the fender. (see image of the ruler, with the horizontal plate at the highest ridge of the strut panel)
- the 4 connecting parts that are missing, wouldn't even fit between the inner fender and the inside edge of the outer fender. They seem to be about
the same 7 mm higher then the available space.
My question to the gruppe:
- Who can measure this distance on their car; providing their car hasn't been chopped up? It is measured by placing a flat plate on the highest edge of the strut tower, and extending that plane to the outside fender. what is then the distance to the edge of the raingutter of the fender? In my car it is 10 mm below as in the pic.
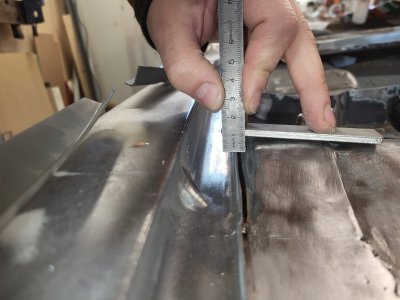
fyi;
Here is the Stainless steel bodied E9. It seems to show that the highest edge of the strut lies is just above the raingutter edge of the fender (but the angle of the pic should be more horizontal to be sure):
some images from the web/Lezebre that are difficult to interpretate: From these pics I find it hard to estimate how high the lines are relative to each other.
If i take a guess; we'll see differences: the green car below shows clearly that the strut tower lies below the edge of the fender as it clearly exhibits an opening.
But I do not see this in other cars. (note: I have little info which cars have been rebuild during their lifetime)
This yellow car, like mine, i missing the 2 right hand connection parts between the inner and outer fender; but the strut lies clearly BELOW the outer fender.
and some other cars (CSL, from Lezebre)
this white one is documented to have new fenders: